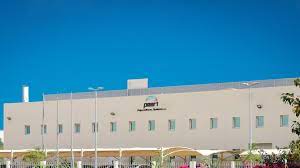
The Versatile World of Polyurethane Systems
Polyurethane systems have revolutionized various industries with their versatility, durability, and performance. From insulation to coatings, adhesives to sealants, polyurethane systems offer a wide range of applications that cater to diverse needs.
Insulation
One of the key areas where polyurethane systems excel is in thermal insulation. Polyurethane foam, known for its high insulating properties, is widely used in buildings, refrigeration units, and appliances to reduce energy consumption and maintain optimal temperature levels.
Coatings
Polyurethane coatings provide protective layers that are resistant to abrasion, chemicals, and weathering. These coatings are commonly used in automotive finishes, industrial equipment coatings, and flooring applications due to their excellent durability and aesthetic appeal.
Adhesives and Sealants
Polyurethane adhesives offer strong bonds across various substrates such as metals, plastics, wood, and composites. They are favored for their fast curing times and high strength properties. Polyurethane sealants provide effective sealing against moisture, air leakage, and sound transmission in construction and automotive applications.
Custom Formulations
With advancements in technology, polyurethane systems can be customized to meet specific requirements. By adjusting the chemical composition and processing parameters, manufacturers can tailor polyurethane products to achieve desired performance characteristics for a wide range of applications.
Sustainability
In recent years, there has been a growing emphasis on developing sustainable polyurethane systems. Manufacturers are exploring bio-based raw materials and eco-friendly production processes to reduce environmental impact while maintaining the performance benefits of polyurethanes.
Overall, polyurethane systems continue to play a crucial role in enhancing product performance, efficiency, and sustainability across industries. Their adaptability and versatility make them a preferred choice for manufacturers looking to innovate and meet evolving market demands.
Exploring Polyurethane Systems: Applications, Advantages, and Sustainability Considerations
- What are polyurethane systems?
- How are polyurethane systems used in insulation?
- What are the advantages of using polyurethane coatings?
- How do polyurethane adhesives differ from other types of adhesives?
- What industries commonly use polyurethane sealants?
- Are there different types of polyurethane systems available?
- What considerations should be made when selecting a polyurethane system for a specific application?
- How can sustainability be integrated into the production of polyurethane systems?
- What are the key factors influencing the performance and durability of polyurethane systems?
What are polyurethane systems?
Polyurethane systems refer to a versatile class of materials that encompass a wide range of products used in various industries for insulation, coatings, adhesives, sealants, and more. These systems typically consist of two main components – polyols and isocyanates – that react together to form polymers with unique properties. Polyurethane systems offer exceptional durability, flexibility, and performance characteristics, making them suitable for diverse applications. Whether it’s providing thermal insulation in buildings, protecting surfaces with coatings, or bonding materials with adhesives, polyurethane systems play a vital role in enhancing product quality and efficiency across different sectors.
How are polyurethane systems used in insulation?
Polyurethane systems are commonly used in insulation due to their exceptional thermal properties and versatility. In the insulation industry, polyurethane foam is a popular choice for providing effective thermal insulation in buildings, refrigeration units, appliances, and more. The unique structure of polyurethane foam allows it to create a tight seal that minimizes heat transfer, resulting in energy efficiency and cost savings. By filling gaps and voids with polyurethane foam insulation, buildings can maintain consistent indoor temperatures, reduce energy consumption for heating and cooling, and enhance overall comfort levels. The ease of application and ability to conform to various shapes make polyurethane systems a preferred option for insulating a wide range of structures effectively.
What are the advantages of using polyurethane coatings?
Polyurethane coatings offer a multitude of advantages that make them a popular choice in various industries. These coatings provide exceptional durability, resistance to abrasion, chemicals, and weathering, ensuring long-lasting protection for surfaces. Additionally, polyurethane coatings exhibit excellent adhesion to different substrates, allowing for versatile applications across diverse materials. Their fast curing times and high gloss finishes enhance productivity and aesthetics in automotive finishes, industrial equipment coatings, and flooring systems. Moreover, polyurethane coatings can be customized to meet specific performance requirements, making them a versatile solution for achieving desired properties such as UV resistance, flexibility, or hardness. Overall, the advantages of using polyurethane coatings lie in their ability to deliver superior protection, aesthetics, and performance for a wide range of applications.
How do polyurethane adhesives differ from other types of adhesives?
Polyurethane adhesives stand out from other types of adhesives due to their exceptional bonding strength, versatility, and durability. Unlike traditional adhesives, polyurethane adhesives offer a strong bond that can withstand high loads and harsh environmental conditions. They adhere well to a wide range of substrates, including metals, plastics, wood, and composites, making them suitable for diverse applications. Additionally, polyurethane adhesives have fast curing times and exhibit excellent resistance to moisture, chemicals, and temperature fluctuations. These unique properties make polyurethane adhesives a preferred choice for applications where reliable bonding performance is essential.
What industries commonly use polyurethane sealants?
Polyurethane sealants find extensive use across various industries due to their versatile sealing properties and durability. Common industries that rely on polyurethane sealants include construction, automotive, aerospace, marine, and manufacturing. In the construction sector, polyurethane sealants are utilized for sealing joints, gaps, and cracks in buildings, bridges, and infrastructure to prevent water infiltration and air leakage. In the automotive industry, these sealants are employed for bonding components, weatherproofing vehicles, and providing structural integrity. Aerospace and marine industries also benefit from the superior adhesion and resistance of polyurethane sealants in demanding environments. Additionally, manufacturers across different sectors use polyurethane sealants for assembly processes and product finishing to ensure quality and longevity.
Are there different types of polyurethane systems available?
Yes, there are different types of polyurethane systems available to cater to a wide range of applications and requirements. The versatility of polyurethane allows for the formulation of various systems with distinct properties and characteristics. Some common types include flexible foams used in mattresses and upholstery, rigid foams for insulation and structural applications, coatings for protection and aesthetics, adhesives for bonding different materials, sealants for sealing joints and gaps, elastomers for durable rubber-like products, and integral skin foams for soft-touch surfaces. Each type of polyurethane system is designed to meet specific needs in terms of performance, durability, flexibility, and other attributes, offering manufacturers a diverse toolkit to address different challenges across industries.
What considerations should be made when selecting a polyurethane system for a specific application?
When selecting a polyurethane system for a specific application, several key considerations should be taken into account to ensure optimal performance and desired outcomes. Firstly, understanding the requirements of the application, such as mechanical properties, chemical resistance, durability, and environmental factors, is essential. The compatibility of the polyurethane system with substrates and other materials involved in the application should also be evaluated to prevent any potential issues. Additionally, considering factors like processing conditions, curing time, and cost-effectiveness can help in choosing the most suitable polyurethane system that meets both technical specifications and budget constraints. Conducting thorough testing and seeking expert advice can further aid in making an informed decision for selecting the right polyurethane system for a specific application.
How can sustainability be integrated into the production of polyurethane systems?
Integrating sustainability into the production of polyurethane systems involves a multi-faceted approach that addresses environmental impact, resource efficiency, and product lifecycle. One key strategy is to explore the use of bio-based raw materials derived from renewable sources, reducing reliance on fossil fuels and lowering carbon footprint. Additionally, optimizing production processes to minimize waste generation, energy consumption, and emissions can contribute to a more sustainable manufacturing practice. Implementing closed-loop systems for recycling and reusing materials can further enhance the eco-friendliness of polyurethane production. Collaborating with stakeholders across the supply chain to promote transparency, responsible sourcing, and eco-friendly practices is essential in creating a sustainable ecosystem for polyurethane systems.
What are the key factors influencing the performance and durability of polyurethane systems?
Several key factors influence the performance and durability of polyurethane systems. The quality of raw materials used in the formulation, including polyols, isocyanates, additives, and catalysts, plays a significant role in determining the final properties of the polyurethane product. Proper mixing ratios and processing conditions are crucial for achieving optimal performance and ensuring uniformity in the final product. Environmental factors such as temperature, humidity, and exposure to UV light can impact the long-term durability of polyurethane systems. Additionally, proper surface preparation and application techniques are essential to maximize adhesion and performance of polyurethane coatings and sealants. Regular maintenance and adherence to recommended usage guidelines also contribute to extending the lifespan and effectiveness of polyurethane systems.