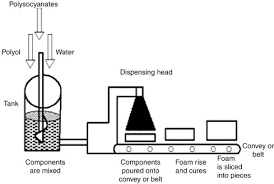
The Process of Polyurethane Manufacturing
Polyurethane is a versatile polymer that is used in a wide range of applications, from insulation and furniture to automotive parts and footwear. The manufacturing process of polyurethane involves several key steps that transform raw materials into the final product.
Step 1: Prepolymer Formation
The first step in polyurethane manufacturing is the formation of a prepolymer. This involves reacting a polyol with an isocyanate to create a material with reactive end groups. The ratio of polyol to isocyanate used in this step determines the properties of the final polyurethane.
Step 2: Mixing and Processing
Once the prepolymer is formed, it is mixed with other additives such as catalysts, surfactants, and blowing agents. This mixture is then processed using techniques like pouring, spraying, or molding to give shape to the polyurethane product.
Step 3: Curing and Solidification
After processing, the polyurethane undergoes a curing process where it solidifies into its final form. This can involve exposure to heat or ambient conditions depending on the specific type of polyurethane being manufactured.
Step 4: Finishing and Quality Control
Once the polyurethane product has solidified, it may undergo finishing processes such as cutting, trimming, or painting to achieve the desired appearance and dimensions. Quality control checks are also performed at this stage to ensure that the product meets industry standards.
Applications of Polyurethane
Polyurethane finds use in a wide variety of industries due to its excellent mechanical properties, durability, and versatility. Common applications include insulation materials, adhesives, sealants, coatings, automotive parts, furniture cushions, and footwear components.
Conclusion
The manufacturing process of polyurethane involves precise control over chemical reactions and processing techniques to create products with diverse properties and applications. As technology advances, new formulations and production methods continue to expand the possibilities for this important polymer.
8 Essential Safety and Quality Tips for Polyurethane Manufacturing Excellence
- Ensure proper ventilation in the manufacturing area to prevent exposure to harmful fumes.
- Follow safety protocols when handling chemicals used in polyurethane production.
- Maintain equipment regularly to ensure efficient and safe operation.
- Monitor and control temperature and humidity levels for optimal production conditions.
- Use appropriate personal protective equipment (PPE) such as gloves, goggles, and masks.
- Train employees on proper handling procedures and emergency protocols.
- Implement quality control measures to ensure consistency in product performance.
- Properly store raw materials to prevent contamination or degradation.
Ensure proper ventilation in the manufacturing area to prevent exposure to harmful fumes.
Proper ventilation in the manufacturing area is crucial to prevent exposure to harmful fumes during the polyurethane manufacturing process. Adequate ventilation helps in maintaining a safe and healthy work environment by removing potentially hazardous gases and vapors that may be released during the production of polyurethane products. Implementing effective ventilation systems not only protects the health of workers but also ensures compliance with safety regulations, promoting a sustainable and responsible approach to polyurethane manufacturing.
Follow safety protocols when handling chemicals used in polyurethane production.
It is crucial to follow safety protocols when handling chemicals used in polyurethane production. Many chemicals involved in the manufacturing process can be hazardous if not handled properly. Workers should wear appropriate protective gear such as gloves, goggles, and masks to prevent exposure to harmful substances. Proper ventilation and storage of chemicals are also essential to minimize risks. By prioritizing safety protocols, we can ensure a secure working environment for all individuals involved in polyurethane manufacturing.
Maintain equipment regularly to ensure efficient and safe operation.
Regular maintenance of equipment is crucial in polyurethane manufacturing to ensure efficient and safe operation. By conducting routine inspections, cleaning, and servicing of machinery, manufacturers can prevent unexpected breakdowns, optimize performance, and extend the lifespan of their equipment. Proper maintenance also helps in identifying potential safety hazards early on, reducing the risk of accidents in the workplace. Overall, investing time and resources in keeping equipment in top condition not only improves productivity but also prioritizes the well-being of workers involved in the manufacturing process.
Monitor and control temperature and humidity levels for optimal production conditions.
Monitoring and controlling temperature and humidity levels is crucial for ensuring optimal production conditions in polyurethane manufacturing. Fluctuations in temperature and humidity can impact the chemical reactions involved in the process, leading to variations in product quality and performance. By maintaining stable and controlled environmental conditions, manufacturers can achieve consistent results, improve efficiency, and enhance the overall quality of the polyurethane products being produced. This attention to detail helps to minimize waste, reduce production errors, and ultimately deliver high-quality polyurethane materials that meet industry standards.
Use appropriate personal protective equipment (PPE) such as gloves, goggles, and masks.
It is crucial to prioritize safety in polyurethane manufacturing by using appropriate personal protective equipment (PPE) such as gloves, goggles, and masks. These items act as a barrier between workers and potentially hazardous chemicals, ensuring their protection from skin contact, eye irritation, and inhalation of fumes or particles. By wearing the necessary PPE, workers can minimize the risks associated with handling polyurethane materials and maintain a safe working environment conducive to efficient production processes.
Train employees on proper handling procedures and emergency protocols.
It is crucial to train employees on proper handling procedures and emergency protocols in polyurethane manufacturing facilities. By providing comprehensive training, workers can understand the potential hazards associated with working with polyurethane materials and learn how to safely handle them. In the event of an emergency, such as a spill or chemical exposure, well-trained employees will be equipped to respond quickly and effectively, minimizing risks to themselves and others in the workplace. Regular training sessions also help reinforce best practices and ensure a culture of safety within the manufacturing environment.
Implement quality control measures to ensure consistency in product performance.
Implementing quality control measures is crucial in polyurethane manufacturing to guarantee consistency in product performance. By closely monitoring and evaluating each stage of the production process, manufacturers can identify and rectify any deviations that may affect the final product’s quality. This proactive approach not only helps maintain uniformity in properties such as strength, durability, and appearance but also enhances customer satisfaction by delivering reliable and high-performing polyurethane products consistently.
Properly store raw materials to prevent contamination or degradation.
Proper storage of raw materials is crucial in polyurethane manufacturing to prevent contamination or degradation of the ingredients. Maintaining the quality of polyols, isocyanates, catalysts, and other additives ensures that the final polyurethane product meets desired specifications and performance standards. By storing raw materials in controlled environments with appropriate temperature, humidity, and ventilation conditions, manufacturers can safeguard the integrity of their supplies and uphold the quality of their production processes.