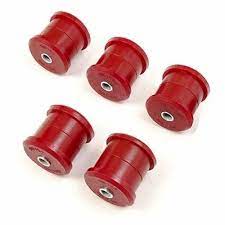
Polyurethane Automotive Applications in India
Polyurethane, a versatile and durable material, is increasingly finding its way into various applications in the automotive industry in India. From enhancing vehicle aesthetics to improving performance and safety, polyurethane is revolutionizing the way vehicles are designed and manufactured.
Lightweight Components
One of the key advantages of using polyurethane in automotive applications is its lightweight nature. By replacing traditional materials with polyurethane components, manufacturers can reduce the overall weight of vehicles, leading to improved fuel efficiency and lower emissions.
Bumpers and Body Panels
Polyurethane is commonly used in the production of bumpers and body panels due to its impact resistance and ability to withstand harsh environmental conditions. These components not only enhance the aesthetic appeal of vehicles but also provide added protection in case of collisions.
Seating and Interior Trim
The comfort and aesthetics of vehicle interiors are greatly enhanced by the use of polyurethane in seating and interior trim applications. Polyurethane foam provides excellent cushioning properties, ensuring a comfortable ride for passengers while maintaining durability over time.
Insulation and Soundproofing
Polyurethane foams are widely used for insulation and soundproofing purposes in automotive applications. By incorporating polyurethane insulation materials, manufacturers can improve thermal efficiency within vehicles while reducing noise levels for a quieter driving experience.
Adhesives and Sealants
Polyurethane-based adhesives and sealants play a crucial role in bonding various components together during the assembly process. These adhesives offer strong bonding properties, ensuring structural integrity and longevity for different parts of the vehicle.
In conclusion, polyurethane has become an indispensable material in the automotive industry in India, offering a wide range of benefits across different applications. As technology continues to advance, we can expect to see further innovations that leverage the unique properties of polyurethane to drive efficiency, sustainability, and performance in vehicles.
Driving Innovation: The Advantages of Polyurethane in India’s Automotive Industry
- Enhances fuel efficiency by reducing overall vehicle weight
- Provides impact resistance and durability for bumpers and body panels
- Improves comfort and aesthetics in seating and interior trim applications
- Offers excellent insulation and soundproofing properties for a quieter ride
- Ensures strong bonding and structural integrity through polyurethane adhesives
Challenges of Polyurethane in Indian Automotive Applications: Cost, Sustainability, and Health Concerns
- Higher initial cost compared to traditional materials
- Limited color options for aesthetic customization
- Susceptible to degradation from UV exposure over time
- Difficulties in recycling and disposal at end of life
- Potential health concerns during manufacturing due to chemical exposure
- May require specialized equipment and expertise for repair and maintenance
Enhances fuel efficiency by reducing overall vehicle weight
Polyurethane’s contribution to enhancing fuel efficiency in automotive applications in India is significant, primarily due to its ability to reduce the overall weight of vehicles. By replacing heavier materials with lightweight polyurethane components, manufacturers can achieve substantial weight savings without compromising on strength or durability. This reduction in vehicle weight not only leads to improved fuel efficiency but also helps lower emissions, making polyurethane an essential element in the quest for sustainable and eco-friendly transportation solutions in the country.
Provides impact resistance and durability for bumpers and body panels
Polyurethane’s ability to provide exceptional impact resistance and durability makes it an ideal choice for bumpers and body panels in automotive applications in India. By incorporating polyurethane components, vehicles benefit from enhanced protection against collisions and harsh environmental conditions, ensuring longevity and structural integrity. This pro of polyurethane not only improves the safety of vehicles but also contributes to their aesthetic appeal, showcasing the versatility and reliability of polyurethane in the automotive industry.
Improves comfort and aesthetics in seating and interior trim applications
Polyurethane plays a significant role in enhancing comfort and aesthetics in seating and interior trim applications within the automotive industry in India. The use of polyurethane foam in vehicle interiors provides superior cushioning, ensuring a comfortable and luxurious experience for passengers. Additionally, polyurethane materials offer versatility in design, allowing for customized interior trim options that elevate the overall aesthetic appeal of vehicles. By incorporating polyurethane in seating and interior trim applications, automotive manufacturers can create interiors that not only look visually appealing but also prioritize passenger comfort and satisfaction.
Offers excellent insulation and soundproofing properties for a quieter ride
Polyurethane automotive applications in India offer excellent insulation and soundproofing properties, contributing to a quieter and more comfortable ride for passengers. By using polyurethane foams for insulation, vehicles can better regulate internal temperatures, enhancing overall thermal efficiency. Additionally, the soundproofing capabilities of polyurethane help reduce external noise levels inside the vehicle, creating a peaceful environment for occupants to enjoy their journey without disturbances from road noise or outside elements.
Ensures strong bonding and structural integrity through polyurethane adhesives
Polyurethane adhesives play a crucial role in ensuring strong bonding and structural integrity in automotive applications in India. These adhesives offer exceptional bonding properties that help securely attach various components together during the assembly process. By using polyurethane adhesives, manufacturers can create durable bonds that withstand the rigors of daily vehicle use, contributing to the overall safety and longevity of the vehicle. The reliable performance of polyurethane adhesives underscores their importance in maintaining the structural integrity of automotive components, enhancing both the safety and quality of vehicles on Indian roads.
Higher initial cost compared to traditional materials
One significant drawback of using polyurethane in automotive applications in India is the higher initial cost compared to traditional materials. While polyurethane offers numerous advantages such as lightweight properties, durability, and design flexibility, the upfront investment required for incorporating polyurethane components into vehicles can be a deterrent for manufacturers. This higher cost may pose a challenge for companies looking to adopt polyurethane solutions, especially in a price-sensitive market like India where cost-effectiveness plays a crucial role in decision-making.
Limited color options for aesthetic customization
While polyurethane offers numerous advantages in automotive applications in India, one notable drawback is the limited color options available for aesthetic customization. Unlike some other materials that allow for a wide range of color choices, polyurethane can be more challenging to customize in terms of color. This limitation may restrict designers and manufacturers in achieving specific aesthetic preferences or branding requirements for vehicles. Despite this con, innovative solutions such as coatings or painting techniques can still be employed to enhance the visual appeal of polyurethane components in automotive design.
Susceptible to degradation from UV exposure over time
Polyurethane automotive applications in India are not without their challenges, with one notable downside being their susceptibility to degradation from UV exposure over time. The ultraviolet rays from the sun can cause polyurethane materials to deteriorate, leading to discoloration, brittleness, and reduced structural integrity. This degradation can impact the longevity and performance of polyurethane components in vehicles, necessitating proper maintenance and protective measures to mitigate the effects of UV exposure and ensure the durability of these automotive applications in the Indian climate.
Difficulties in recycling and disposal at end of life
One significant challenge associated with polyurethane automotive applications in India is the difficulties in recycling and disposal at the end of their life cycle. Polyurethane materials are known for their durability and longevity, making them less biodegradable compared to other materials. This poses a concern for environmental sustainability as the proper disposal of polyurethane components can be complex and costly. Finding efficient recycling methods for polyurethane automotive parts remains a key area of focus to minimize environmental impact and promote a circular economy within the automotive industry in India.
Potential health concerns during manufacturing due to chemical exposure
One significant con associated with polyurethane automotive applications in India is the potential health concerns that arise during the manufacturing process due to chemical exposure. The production of polyurethane involves the use of various chemicals, some of which may be hazardous if not handled properly. Workers involved in manufacturing polyurethane components may be at risk of exposure to these chemicals, leading to potential health issues such as respiratory problems, skin irritations, and other adverse effects. It is crucial for manufacturers to implement strict safety measures and provide adequate training to mitigate these risks and ensure a safe working environment for all employees involved in the production process.
May require specialized equipment and expertise for repair and maintenance
One significant drawback of polyurethane automotive applications in India is that they may require specialized equipment and expertise for repair and maintenance. Unlike traditional materials, repairing or replacing polyurethane components often necessitates specific tools and knowledge that may not be readily available to all mechanics or service centers. This can lead to increased costs and longer downtimes for vehicle owners, making maintenance more complex and potentially limiting accessibility to repairs in certain regions.