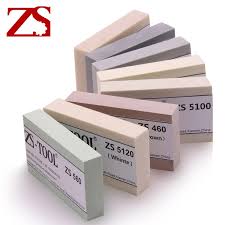
The Art of Casting Rigid Polyurethane Foam
When it comes to creating lightweight, durable, and versatile products, casting rigid polyurethane foam is a popular choice among manufacturers. This process involves pouring a mixture of polyol and isocyanate into a mold, where it expands and cures to form a solid foam with excellent thermal insulation properties.
Benefits of Rigid Polyurethane Foam Casting
Rigid polyurethane foam offers numerous advantages, making it ideal for a wide range of applications. Some key benefits include:
- High strength-to-weight ratio
- Excellent thermal insulation
- Chemical resistance
- Durable and long-lasting
- Versatile in shape and size
The Casting Process
The process of casting rigid polyurethane foam involves several steps to ensure the quality and consistency of the final product:
- Preparation of the mold: The mold is prepared by applying release agents to prevent the foam from sticking.
- Mixing components: The polyol and isocyanate components are carefully measured and mixed together to initiate the foaming reaction.
- Pouring into the mold: The mixed components are poured into the prepared mold, where they expand to fill the cavity.
- Curing: The foam cures at room temperature or under controlled conditions to achieve the desired hardness and density.
- Construction: Insulation panels, decorative elements, and structural components.
- Automotive: Lightweight parts for vehicles that require high strength and impact resistance.
- Furniture: Molded furniture pieces with intricate designs and durability.
- Marine: Buoyancy materials for boats and watercraft.
- Wear appropriate personal protective equipment, such as gloves and safety goggles, when handling polyurethane foam.
- Ensure the mixing ratio of the polyol and isocyanate components is accurate to achieve the desired foam properties.
- Use a clean and dry mold to prevent any contaminants from affecting the foam’s quality.
- Allow sufficient curing time as per the manufacturer’s instructions before demolding the foam to avoid deformation.
- Consider using a release agent in the mold to facilitate easy removal of the cured foam.
- Dispose of any unused or excess materials properly according to local regulations.
Applications of Rigid Polyurethane Foam Casting
Rigid polyurethane foam casting finds wide application across various industries, including:
Conclusion
Casting rigid polyurethane foam offers manufacturers a cost-effective way to produce high-quality products with exceptional performance characteristics. With its versatility, durability, and insulation properties, rigid polyurethane foam continues to be a material of choice in various industries.
Six Essential Tips for Successful Casting with Rigid Polyurethane Foam
Wear appropriate personal protective equipment, such as gloves and safety goggles, when handling polyurethane foam.
It is crucial to prioritize safety when working with casting rigid polyurethane foam. Always remember to wear appropriate personal protective equipment, such as gloves and safety goggles, when handling polyurethane foam. These safety gear items help protect your skin and eyes from potential exposure to chemicals and ensure a safe working environment. By taking simple precautions like wearing gloves and safety goggles, you can prevent accidents and minimize risks associated with working with polyurethane foam.
Ensure the mixing ratio of the polyol and isocyanate components is accurate to achieve the desired foam properties.
For successful casting of rigid polyurethane foam, it is crucial to ensure that the mixing ratio of the polyol and isocyanate components is accurate. This precise ratio plays a significant role in determining the properties of the foam, including its density, strength, and thermal insulation capabilities. By maintaining the correct proportion of these components, manufacturers can achieve the desired foam properties and ensure consistent quality in their final products.
Use a clean and dry mold to prevent any contaminants from affecting the foam’s quality.
When casting rigid polyurethane foam, it is crucial to use a clean and dry mold to ensure the quality of the final product. Contaminants such as dust, moisture, or residue can negatively impact the foam’s properties and appearance. By maintaining a clean and dry mold, manufacturers can prevent any unwanted substances from interfering with the foaming process, resulting in consistent and high-quality foam products that meet the desired specifications.
Allow sufficient curing time as per the manufacturer’s instructions before demolding the foam to avoid deformation.
For successful casting of rigid polyurethane foam, it is crucial to allow sufficient curing time as per the manufacturer’s instructions before demolding the foam. Rushing the demolding process can lead to deformation of the foam and compromise its structural integrity. Patience in allowing the foam to fully cure ensures that it attains the desired hardness and density, resulting in a high-quality final product that meets performance expectations.
Consider using a release agent in the mold to facilitate easy removal of the cured foam.
When casting rigid polyurethane foam, it is advisable to consider using a release agent in the mold to facilitate the easy removal of the cured foam. A release agent helps prevent the foam from sticking to the mold, allowing for smooth extraction without damaging the final product. By applying a release agent before pouring the foam mixture, manufacturers can ensure a clean and effortless demolding process, thereby enhancing efficiency and maintaining the integrity of the cast foam components.
Dispose of any unused or excess materials properly according to local regulations.
It is crucial to dispose of any unused or excess materials from casting rigid polyurethane foam properly, in accordance with local regulations. Improper disposal of polyurethane foam components can have harmful effects on the environment and human health. By following the guidelines set forth by local authorities, manufacturers can ensure that waste materials are handled responsibly, minimizing the impact on the ecosystem and promoting a sustainable production process.