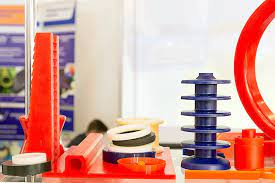
The Versatility of Cast Polyurethane Products
Cast polyurethane products have gained popularity across various industries due to their exceptional versatility, durability, and performance. These products are created through a casting process that allows for the customization of shapes, sizes, hardness levels, and colors to meet specific application requirements.
Applications in Various Industries
From industrial machinery components to automotive parts, cast polyurethane products find applications in a wide range of industries. Their ability to withstand harsh environments, resist abrasion and impact, and provide excellent load-bearing capacity makes them ideal for demanding applications.
Advantages of Cast Polyurethane Products
One of the key advantages of cast polyurethane products is their ability to be tailored to meet specific performance criteria. Whether it’s creating wear-resistant rollers for material handling equipment or producing impact-absorbing bumpers for automotive safety systems, cast polyurethane offers unmatched flexibility in design and functionality.
Environmental Benefits
In addition to their superior performance characteristics, cast polyurethane products also offer environmental benefits. They can be recycled and repurposed, reducing waste and contributing to sustainability efforts in manufacturing processes.
Conclusion
Cast polyurethane products continue to revolutionize various industries with their versatility, durability, and environmental advantages. As technology advances and demand for high-performance materials grows, the role of cast polyurethane in shaping the future of manufacturing remains significant.
5 Essential Tips for Superior Cast Polyurethane Products: Achieving Optimal Performance and Quality
- Ensure proper mixing ratio of polyurethane components for best results.
- Use appropriate mold release agents to easily remove cast polyurethane parts from molds.
- Allow sufficient curing time as per manufacturer’s instructions for optimal strength and durability.
- Consider post-curing the polyurethane parts for enhanced properties such as hardness and heat resistance.
- Avoid moisture contamination during the casting process to prevent defects in the final products.
Ensure proper mixing ratio of polyurethane components for best results.
Ensuring the proper mixing ratio of polyurethane components is crucial for achieving the best results when working with cast polyurethane products. The correct ratio ensures that the chemical reaction between the components occurs as intended, leading to optimal physical properties such as hardness, flexibility, and durability. Deviating from the recommended mixing ratio can result in inconsistencies in product performance, affecting quality and longevity. Therefore, meticulous attention to detail during the mixing process is essential to harness the full potential of cast polyurethane products.
Use appropriate mold release agents to easily remove cast polyurethane parts from molds.
Using appropriate mold release agents is crucial when working with cast polyurethane products to ensure easy removal of the finished parts from molds. These agents help prevent the polyurethane material from sticking to the mold surface, facilitating a smooth release process and preventing damage to the final product. By choosing the right mold release agent for the specific type of polyurethane being used, manufacturers can enhance efficiency in production and maintain the quality of their cast polyurethane parts.
Allow sufficient curing time as per manufacturer’s instructions for optimal strength and durability.
It is crucial to allow sufficient curing time as per the manufacturer’s instructions when working with cast polyurethane products to ensure optimal strength and durability. Proper curing time allows the material to fully set and develop its desired properties, such as hardness and resilience. Rushing the curing process can compromise the quality of the final product and may lead to performance issues down the line. By following the manufacturer’s guidelines for curing time, you can maximize the strength and durability of cast polyurethane products, ensuring they meet or exceed expectations in various applications.
Consider post-curing the polyurethane parts for enhanced properties such as hardness and heat resistance.
Consider post-curing the cast polyurethane parts to enhance their properties, such as hardness and heat resistance. Post-curing involves subjecting the polyurethane parts to additional heat treatment after the initial curing process. This extra step can improve the overall performance and durability of the parts, making them better suited for applications that require higher levels of hardness and thermal stability. By carefully controlling the post-curing process, manufacturers can optimize the material properties of cast polyurethane products to meet specific requirements and ensure superior performance in demanding environments.
Avoid moisture contamination during the casting process to prevent defects in the final products.
One crucial tip for ensuring the quality of cast polyurethane products is to avoid moisture contamination during the casting process. Moisture can lead to defects in the final products, compromising their performance and durability. By maintaining a dry environment and using proper sealing techniques, manufacturers can prevent issues such as bubbles, delamination, and reduced mechanical properties in cast polyurethane components. Implementing strict controls to minimize moisture intrusion is essential for achieving high-quality end products that meet the desired specifications and performance standards.