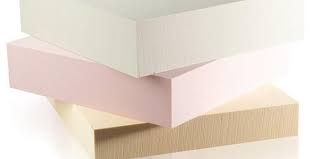
The Importance of Rigid Polyurethane Foam Density in Applications
Rigid polyurethane foam is a versatile material known for its thermal insulation properties, structural strength, and lightweight nature. One crucial factor that significantly impacts the performance of rigid polyurethane foam is its density.
The density of rigid polyurethane foam refers to the mass per unit volume of the material. It is typically measured in kilograms per cubic meter (kg/m³). Higher density foams have more material packed into a given volume, resulting in increased strength and durability.
Here are some key points highlighting the importance of rigid polyurethane foam density in various applications:
Thermal Insulation:
Higher density foams have smaller, more closely packed cells, which reduce heat transfer through conduction. This property makes high-density rigid polyurethane foam an excellent choice for thermal insulation in buildings, refrigeration units, and other applications where energy efficiency is essential.
Structural Support:
Rigid polyurethane foam with higher density offers greater structural support and load-bearing capacity. This makes it suitable for use in construction elements such as wall panels, roofing systems, and composite materials where strength and stability are critical.
Dimensional Stability:
The density of rigid polyurethane foam also affects its dimensional stability. Higher density foams are less prone to shrinkage or expansion over time, ensuring that the material maintains its shape and properties under varying conditions.
Processing and Cost Considerations:
While higher density foams offer superior performance characteristics, they may require specialized processing equipment and techniques. Additionally, the cost of high-density rigid polyurethane foam may be higher compared to lower density options due to the increased material content.
In conclusion, understanding the role of rigid polyurethane foam density is crucial for selecting the right material for specific applications. By considering factors such as thermal insulation requirements, structural needs, dimensional stability, processing capabilities, and cost considerations, manufacturers can optimize the performance and efficiency of their products utilizing rigid polyurethane foam.
7 Essential Tips for Choosing the Right Rigid Polyurethane Foam Density
- Higher foam density typically results in better mechanical properties.
- Lower foam density usually means better insulation properties.
- Foam density affects the weight of the final product.
- Ensure proper mixing ratios for consistent foam density.
- Higher densities may require longer curing times.
- Consider the application requirements when selecting foam density.
- Foam density impacts cost, so choose wisely based on needs.
Higher foam density typically results in better mechanical properties.
Higher foam density in rigid polyurethane foam is often associated with improved mechanical properties. This means that foams with higher density tend to offer greater strength, durability, and load-bearing capacity compared to lower density counterparts. The closer packing of material in high-density foams results in enhanced structural integrity, making them ideal for applications where mechanical performance is a key consideration. By choosing rigid polyurethane foam with higher density, manufacturers can ensure that their products meet the required mechanical specifications and deliver superior performance in various structural and insulation applications.
Lower foam density usually means better insulation properties.
Lower foam density in rigid polyurethane foam typically translates to better insulation properties. This is because lower density foams have larger, more open cells that trap more air, which is a poor conductor of heat. As a result, these foams offer improved thermal resistance, making them ideal for applications where high levels of insulation are required. However, it is important to balance density with structural integrity and other performance factors to ensure the foam meets the specific requirements of the intended application.
Foam density affects the weight of the final product.
The density of rigid polyurethane foam plays a significant role in determining the weight of the final product. Higher foam density results in a denser material with more mass packed into a given volume, leading to increased weight of the finished product. Manufacturers must carefully consider the desired weight requirements and performance characteristics when selecting the appropriate foam density for their applications. By understanding how foam density influences the weight of the final product, companies can make informed decisions to achieve optimal results in terms of structural integrity, thermal insulation, and overall product performance.
Ensure proper mixing ratios for consistent foam density.
Proper mixing ratios are essential to achieve consistent foam density in rigid polyurethane applications. Maintaining the correct balance between the polyol and isocyanate components during the mixing process is crucial for achieving the desired foam properties. Deviating from the recommended ratios can lead to variations in density, affecting the structural integrity and thermal performance of the foam. By ensuring precise mixing ratios are followed diligently, manufacturers can produce high-quality rigid polyurethane foam with uniform density, resulting in reliable and effective end products.
Higher densities may require longer curing times.
Higher densities of rigid polyurethane foam may necessitate longer curing times during the manufacturing process. This is because the increased material content in higher density foams can result in a more intricate cell structure that requires adequate time for complete curing and setting. Manufacturers need to consider this factor while planning production schedules to ensure that the foam achieves optimal physical properties and performance characteristics. Balancing curing time with production efficiency is essential to maintain quality standards when working with high-density rigid polyurethane foam formulations.
Consider the application requirements when selecting foam density.
When choosing the density of rigid polyurethane foam, it is essential to consider the specific requirements of the application. Different applications may demand varying levels of thermal insulation, structural strength, and dimensional stability. By aligning the foam density with the application’s needs, manufacturers can ensure optimal performance and longevity of the end product. Whether it is for building insulation, refrigeration systems, or composite materials, selecting the right foam density based on application requirements is key to achieving desired outcomes.
Foam density impacts cost, so choose wisely based on needs.
Foam density plays a significant role in determining the cost of rigid polyurethane foam, making it essential to choose wisely based on specific needs. Higher density foams generally offer superior performance characteristics but may come at a higher price point due to the increased material content. On the other hand, lower density foams may be more cost-effective but could sacrifice certain properties such as strength and thermal insulation. By carefully assessing the requirements of the intended application and balancing performance with budget considerations, manufacturers can make informed decisions when selecting the optimal foam density for their products.
Thankks foor shaqring such a good thought, post is fastidious, thats why i have read iit entirely
Thank you for taking the time to read the article on rigid polyurethane foam density. We’re glad you found the information valuable and appreciate your positive feedback. If you have any questions or need further clarification on the topic, feel free to ask.