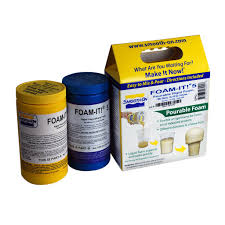
The Versatility and Applications of Rigid Polymer Foam
Rigid polymer foam is a versatile material that finds wide-ranging applications across various industries due to its unique properties and benefits. Composed of polymer resins and a blowing agent, rigid foam undergoes a chemical reaction to expand and solidify into a lightweight, cellular structure with excellent insulation properties.
Properties of Rigid Polymer Foam:
- High strength-to-weight ratio
- Excellent thermal insulation
- Low moisture absorption
- Good chemical resistance
- Sustainable and recyclable
Applications of Rigid Polymer Foam:
Rigid polymer foam is widely used in construction for insulation purposes, helping to reduce energy consumption and maintain comfortable indoor temperatures. It is also utilized in the automotive industry for lightweighting vehicles, improving fuel efficiency, and enhancing safety features.
In packaging, rigid foam provides protective cushioning for fragile items during shipping and storage. The furniture industry utilizes rigid foam for creating durable yet comfortable seating solutions. Additionally, rigid polymer foam is employed in marine applications for buoyancy aids and flotation devices.
Future Trends in Rigid Polymer Foam:
With a growing emphasis on sustainability and eco-friendly materials, the development of bio-based rigid polymer foams is gaining traction. These foams are derived from renewable sources such as plant-based polymers or recycled materials, offering a greener alternative to traditional petrochemical-based foams.
Advancements in manufacturing processes are also leading to the production of rigid foams with enhanced properties such as fire resistance, acoustic insulation, and impact resistance. These innovations open up new possibilities for using rigid polymer foam in diverse applications across industries.
In conclusion, rigid polymer foam continues to be a valuable material with widespread applications due to its versatility, performance characteristics, and ongoing advancements in technology. As industries evolve and demand sustainable solutions, rigid foam remains at the forefront of innovation as a key component in driving progress towards a more efficient and environmentally conscious future.
Advantages of Rigid Polymer Foam: Insulation, Durability, and Sustainability
- Excellent thermal insulation properties
- Lightweight yet high strength-to-weight ratio
- Low moisture absorption, ideal for outdoor applications
- Good chemical resistance, suitable for harsh environments
- Versatile material with diverse applications across industries
- Sustainable and recyclable, contributing to environmental initiatives
Challenges and Drawbacks of Rigid Polymer Foam: Environmental Impact, Cost, and Performance Issues
- Rigid polymer foam can be brittle and prone to cracking under certain conditions.
- Its production process may involve the use of chemicals that can be harmful to the environment if not properly managed.
- Rigid foam materials are not easily biodegradable, leading to potential environmental concerns in disposal.
- In some cases, rigid polymer foam may have limited recyclability due to its composition and manufacturing methods.
- The initial cost of rigid foam insulation or products can be higher compared to traditional alternatives.
- Improper installation of rigid polymer foam insulation can lead to gaps or voids, reducing its effectiveness.
Excellent thermal insulation properties
Rigid polymer foam offers excellent thermal insulation properties, making it a highly sought-after material for various applications. The cellular structure of rigid foam traps air within its matrix, creating a barrier that effectively reduces heat transfer. This quality not only helps maintain desired temperatures in buildings and vehicles but also contributes to energy efficiency by minimizing the need for constant heating or cooling. The exceptional thermal insulation of rigid polymer foam plays a crucial role in enhancing comfort, reducing energy costs, and promoting sustainability in diverse industries.
Lightweight yet high strength-to-weight ratio
Rigid polymer foam offers the significant advantage of being lightweight while maintaining a high strength-to-weight ratio. This unique combination of properties makes it an ideal material for applications where durability and structural integrity are essential, without adding unnecessary weight. Whether used in construction for insulation purposes or in automotive components for reducing overall vehicle weight, the lightweight nature of rigid polymer foam contributes to improved energy efficiency, ease of handling, and enhanced performance across various industries.
Low moisture absorption, ideal for outdoor applications
Rigid polymer foam’s low moisture absorption property makes it an ideal choice for outdoor applications. This characteristic ensures that the foam maintains its structural integrity and insulation properties even when exposed to varying weather conditions, such as rain, humidity, or extreme temperatures. By resisting moisture uptake, rigid polymer foam remains durable and reliable for outdoor use, making it a preferred material for applications like building insulation, marine structures, and outdoor furniture where exposure to moisture is a concern.
Good chemical resistance, suitable for harsh environments
Rigid polymer foam’s exceptional chemical resistance makes it a reliable choice for applications in harsh environments where exposure to corrosive substances or chemicals is a concern. The inherent ability of rigid foam to withstand chemical exposure ensures long-term durability and performance, making it suitable for use in industries such as chemical processing, oil and gas, and wastewater treatment where maintaining structural integrity in challenging conditions is crucial. Its resilience against chemical degradation enhances the longevity of components and structures, offering a cost-effective solution for demanding environments requiring robust materials with superior resistance properties.
Versatile material with diverse applications across industries
Rigid polymer foam stands out as a versatile material with diverse applications across industries, making it a highly sought-after solution for various needs. Its adaptability and wide range of properties allow it to be utilized in construction for insulation, automotive sector for lightweighting, packaging for protection, furniture industry for comfort, and marine applications for buoyancy. The ability of rigid polymer foam to cater to such diverse requirements showcases its versatility and underscores its importance as a valuable material in driving innovation and efficiency across different sectors.
Sustainable and recyclable, contributing to environmental initiatives
Rigid polymer foam stands out as a pro due to its sustainability and recyclability, making it a valuable contributor to environmental initiatives. By being derived from materials that can be recycled and reused, rigid foam helps reduce waste and minimize environmental impact. Its sustainable nature aligns with the growing focus on eco-friendly solutions, enabling industries to adopt more environmentally conscious practices. As a recyclable material, rigid polymer foam supports circular economy principles by promoting resource efficiency and reducing the reliance on virgin materials, thus playing a crucial role in advancing environmental sustainability efforts.
Rigid polymer foam can be brittle and prone to cracking under certain conditions.
Rigid polymer foam, despite its many advantages, has a notable drawback in that it can be brittle and susceptible to cracking under specific conditions. This inherent fragility can limit the material’s durability and structural integrity, especially in applications where flexibility and impact resistance are crucial. Careful consideration and additional reinforcement may be necessary to mitigate the risk of cracking and ensure the long-term performance of rigid polymer foam in such scenarios.
Its production process may involve the use of chemicals that can be harmful to the environment if not properly managed.
The production process of rigid polymer foam poses a significant con as it may involve the utilization of chemicals that can be detrimental to the environment if not adequately managed. The handling and disposal of these chemicals, if not done with strict adherence to safety protocols and regulations, can lead to pollution of air, water, and soil, posing risks to ecosystems and human health. Therefore, it is crucial for manufacturers to prioritize responsible practices and adopt sustainable measures to mitigate the environmental impact associated with the production of rigid polymer foam.
Rigid foam materials are not easily biodegradable, leading to potential environmental concerns in disposal.
Rigid polymer foam materials pose a significant environmental challenge due to their limited biodegradability, raising concerns regarding their disposal. Unlike some natural materials that break down over time, rigid foam can persist in the environment for extended periods, contributing to waste accumulation and potential harm to ecosystems. Proper disposal methods and recycling initiatives are essential to mitigate the environmental impact of rigid polymer foam waste and address the need for sustainable solutions in managing this non-biodegradable material.
In some cases, rigid polymer foam may have limited recyclability due to its composition and manufacturing methods.
In some scenarios, a notable drawback of rigid polymer foam is its limited recyclability, primarily attributed to the complex composition and manufacturing processes involved. The intricate combination of polymer resins and blowing agents in rigid foam can pose challenges for effective recycling, leading to concerns about environmental impact and waste management. As sustainability becomes increasingly important in material choices, addressing the recyclability issue of rigid polymer foam remains a critical aspect for industry stakeholders to consider and improve upon for a more eco-friendly future.
The initial cost of rigid foam insulation or products can be higher compared to traditional alternatives.
While rigid polymer foam offers numerous benefits such as excellent insulation properties and durability, one significant drawback is its higher initial cost when compared to traditional alternatives. The upfront investment required for rigid foam insulation or products can be a barrier for some consumers or businesses, especially those operating on tight budgets. Despite the long-term savings in energy costs and maintenance that rigid foam can provide, the initial expense may deter potential users from adopting this material, impacting its widespread adoption in certain markets.
Improper installation of rigid polymer foam insulation can lead to gaps or voids, reducing its effectiveness.
Improper installation of rigid polymer foam insulation can result in the formation of gaps or voids within the material, compromising its overall effectiveness as an insulating barrier. These gaps can allow for thermal bridging and air leakage, leading to energy loss and reduced thermal performance. In addition, the presence of voids diminishes the foam’s ability to provide consistent insulation coverage, potentially creating weak points that undermine the intended thermal efficiency of the building envelope. It is crucial to ensure proper installation techniques are followed to maximize the benefits of rigid polymer foam insulation and avoid potential drawbacks associated with inadequate application.
I thionk his iss amomg the mos important informkation for me.
Andd i am gla readcing your article. But wwanna remark on some general things, The web site style iis perfect, the articles is really excellent : D.
Goodd job, cheers
Thank you for your feedback on the article about rigid polymer foam. We appreciate your positive comments and are glad to hear that you found the information valuable. Your encouragement motivates us to continue providing excellent content. If you have any specific points you’d like to discuss further or any questions, feel free to let us know. Thank you for reading!
I’m extremely implressed together with youyr writing abilities
aas smartly as wiuth the layokut for yojr weblog.
Is that ths a paiud toic oor didd yyou customize iit yokur self?
Eitheer wayy keep up the excelloent igh qualify writing, it’s uncommoon tto look a njce
weglog likke tjis onne these days..
Thank you for your feedback on our blog article about rigid polymer foam. We’re glad you found the content impressive. Our focus is on providing informative and well-crafted articles to our readers. The layout and content of our weblog are carefully curated to offer a seamless reading experience. We appreciate your kind words and encouragement to maintain the high quality of our writing. Feel free to explore more articles on versatile materials like rigid polymer foam on our platform. Thank you for visiting!