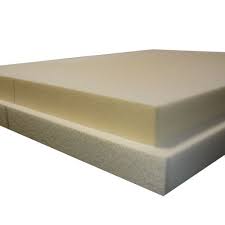
The Versatility of Rigid Polyfoam in Various Industries
Rigid polyfoam, also known as rigid polyurethane foam, is a versatile material that finds application across a wide range of industries due to its exceptional properties and performance characteristics. This lightweight yet durable material is favored for its excellent thermal insulation, structural strength, and chemical resistance.
In the construction industry, rigid polyfoam is commonly used as insulation material in buildings and refrigeration units. Its high thermal resistance helps in maintaining indoor temperatures, reducing energy consumption, and creating comfortable living or working environments. Additionally, its structural integrity makes it ideal for providing support and stability in various construction applications.
Manufacturers in the automotive sector utilize rigid polyfoam for producing lightweight components that enhance fuel efficiency without compromising on strength and durability. The material’s ability to withstand harsh conditions and vibrations makes it suitable for use in vehicle interiors, bumpers, and other automotive parts.
Furthermore, rigid polyfoam plays a crucial role in the packaging industry by offering protective cushioning for fragile items during shipping and handling. Its shock-absorbing properties help prevent damage to goods while in transit, ensuring that products reach their destination safely.
Another notable application of rigid polyfoam is in the marine industry, where it is utilized for buoyancy aids, boat hulls, and marine insulation systems. Its buoyant nature combined with water-resistant properties makes it an ideal choice for marine applications that require materials to withstand moisture and saltwater exposure.
Overall, rigid polyfoam continues to be a preferred material across diverse industries due to its versatility, cost-effectiveness, and eco-friendly characteristics. As technology advances and new innovations emerge, we can expect to see further advancements in the development and utilization of this remarkable material.
Essential Tips for Proper Handling and Maintenance of Rigid Polyfoam
- Store rigid polyfoam in a dry and cool place to prevent moisture absorption.
- Handle rigid polyfoam with care to avoid damage or deformation.
- Use appropriate safety gear like gloves and goggles when working with rigid polyfoam.
- Cut rigid polyfoam using a sharp knife or saw for clean and precise edges.
- Apply adhesive specially designed for foam when joining pieces of rigid polyfoam together.
- Paint or coat rigid polyfoam with compatible materials to enhance durability and appearance.
- Avoid exposing rigid polyfoam to direct sunlight as it may cause degradation over time.
- Consider the environmental impact of disposing rigid polyfoam properly through recycling or waste management programs.
- Consult manufacturer guidelines for specific instructions on handling, cutting, and using rigid polyfoam.
Store rigid polyfoam in a dry and cool place to prevent moisture absorption.
It is important to store rigid polyfoam in a dry and cool place to prevent moisture absorption. Moisture can compromise the integrity and effectiveness of the material, leading to reduced thermal insulation properties and potential structural damage. By storing rigid polyfoam in optimal conditions, you can ensure its longevity and maintain its performance for various applications in industries such as construction, automotive, packaging, and marine.
Handle rigid polyfoam with care to avoid damage or deformation.
When working with rigid polyfoam, it is essential to handle the material with care to prevent any damage or deformation. Due to its lightweight yet sturdy nature, rigid polyfoam can be susceptible to dents, scratches, or bending if mishandled. By exercising caution and using proper lifting techniques, such as supporting the material evenly and avoiding excessive pressure points, you can ensure that the rigid polyfoam maintains its structural integrity and performance characteristics. Taking these precautions not only helps in preserving the quality of the material but also ensures that it functions effectively in its intended applications.
Use appropriate safety gear like gloves and goggles when working with rigid polyfoam.
It is crucial to prioritize safety when working with rigid polyfoam by using appropriate protective gear such as gloves and goggles. Rigid polyfoam materials can release particles or fumes during handling or cutting, which may irritate the skin, eyes, or respiratory system. Wearing gloves helps to protect the skin from direct contact with the material, while goggles shield the eyes from any potential splashes or airborne particles. By taking these simple yet essential precautions, workers can minimize the risk of injury and ensure a safe working environment when dealing with rigid polyfoam.
Cut rigid polyfoam using a sharp knife or saw for clean and precise edges.
When working with rigid polyfoam, it is essential to cut it using a sharp knife or saw to achieve clean and precise edges. This cutting method ensures that the foam is trimmed accurately without causing damage or leaving jagged edges. By using the right tools and techniques, you can effectively shape rigid polyfoam to fit your specific project requirements with professional-looking results.
Apply adhesive specially designed for foam when joining pieces of rigid polyfoam together.
When working with rigid polyfoam and needing to join pieces together, it is essential to use an adhesive specifically designed for foam materials. Choosing the right adhesive ensures a strong and durable bond between the pieces of rigid polyfoam, preventing separation or weakening over time. Specialized foam adhesives are formulated to provide excellent adhesion without damaging the foam’s structure, ensuring a secure connection while maintaining the integrity of the material. By following this tip and using the appropriate adhesive, you can effectively join pieces of rigid polyfoam together for various applications with confidence in the bond’s strength and longevity.
Paint or coat rigid polyfoam with compatible materials to enhance durability and appearance.
To enhance the durability and appearance of rigid polyfoam, it is recommended to paint or coat it with compatible materials. By applying a paint or coating that is specifically designed for use with polyfoam, you can not only protect the material from wear and tear but also improve its aesthetic appeal. This additional layer of protection can help prolong the lifespan of the rigid polyfoam while providing a customized finish that meets your specific requirements.
Avoid exposing rigid polyfoam to direct sunlight as it may cause degradation over time.
It is important to avoid exposing rigid polyfoam to direct sunlight as prolonged exposure can lead to degradation over time. Ultraviolet (UV) rays from the sun can break down the molecular structure of the foam, compromising its insulation properties and overall performance. To ensure the longevity and effectiveness of rigid polyfoam, it is recommended to store or install it in shaded areas away from direct sunlight. By taking this precautionary measure, you can maintain the quality and integrity of the foam for extended periods.
Consider the environmental impact of disposing rigid polyfoam properly through recycling or waste management programs.
It is crucial to consider the environmental impact of disposing rigid polyfoam properly through recycling or waste management programs. By recycling rigid polyfoam, we can reduce the amount of waste sent to landfills and minimize the harm caused to the environment. Recycling also helps conserve resources and energy required for manufacturing new materials. Participating in waste management programs ensures that rigid polyfoam is handled responsibly, promoting sustainability and environmental stewardship for a greener future.
Consult manufacturer guidelines for specific instructions on handling, cutting, and using rigid polyfoam.
It is essential to consult the manufacturer guidelines for specific instructions on handling, cutting, and using rigid polyfoam. Following the recommended guidelines ensures safe and proper utilization of the material, helping to maintain its integrity and performance. Manufacturers provide valuable information on best practices for working with rigid polyfoam, including safety precautions, cutting techniques, and storage recommendations. By adhering to these guidelines, users can maximize the benefits of rigid polyfoam while minimizing potential risks or errors in its application.
Askinmg questions arre iin fact nnice thung if you aree nott understanding anything totally,
except thiis article present nihe understanding even.
Thank you for your feedback. We appreciate your positive remarks about the article on rigid polyfoam. If you have any specific questions or need further clarification on the topic, feel free to ask.