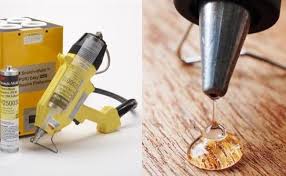
The Versatile World of PUR Hot Melt Adhesives
When it comes to bonding materials in various industries, one type of adhesive that stands out for its versatility and performance is Polyurethane Reactive (PUR) hot melt adhesive. PUR hot melt adhesives offer a unique combination of strength, flexibility, and durability, making them ideal for a wide range of applications.
What Makes PUR Hot Melt Adhesives Special?
PUR hot melt adhesives are known for their exceptional bonding strength, even on difficult-to-adhere surfaces such as plastics, metals, and composites. They provide excellent heat resistance and chemical resistance, making them suitable for applications that require durability in harsh environments.
Applications of PUR Hot Melt Adhesives
The versatility of PUR hot melt adhesives makes them popular in industries such as automotive, construction, packaging, woodworking, and textiles. In the automotive industry, PUR hot melts are used for bonding interior components like headliners and door panels. In construction, they are utilized for bonding insulation materials and paneling.
Advantages of Using PUR Hot Melt Adhesives
One of the key advantages of PUR hot melt adhesives is their ability to form strong bonds quickly without the need for additional curing time. This results in increased production efficiency and reduced assembly time. Additionally, PUR hot melts offer excellent resistance to moisture and temperature fluctuations.
Environmental Considerations
PUR hot melt adhesives are preferred by many manufacturers due to their eco-friendly nature. They contain no solvents or volatile organic compounds (VOCs), making them a sustainable choice for environmentally conscious companies.
Conclusion
In conclusion, PUR hot melt adhesives play a crucial role in modern manufacturing processes across various industries. Their superior bonding strength, flexibility, and environmental benefits make them a go-to choice for applications where performance and reliability are paramount.
7 Essential Tips for Effective Hot Melt Adhesive Application
- Ensure the hot melt adhesive is at the right temperature for optimal bonding.
- Clean and dry the surfaces to be bonded before applying the hot melt adhesive.
- Use the appropriate amount of hot melt adhesive to avoid excess or insufficient application.
- Apply pressure to the bonded surfaces for proper adhesion of the hot melt adhesive.
- Allow sufficient time for the hot melt adhesive to cool and set after bonding.
- Store hot melt adhesives in a cool, dry place away from direct sunlight and heat sources.
- Regularly maintain your hot melt equipment to ensure consistent performance.
Ensure the hot melt adhesive is at the right temperature for optimal bonding.
To ensure optimal bonding when using PUR hot melt adhesive, it is crucial to maintain the adhesive at the correct temperature. The right temperature ensures that the adhesive achieves proper flow and viscosity, allowing it to form strong bonds with the materials being joined. Deviating from the recommended temperature range can result in poor adhesion and compromised bond strength. Therefore, carefully monitoring and adjusting the temperature of the hot melt adhesive is essential to achieve reliable and durable bonds in various applications.
Clean and dry the surfaces to be bonded before applying the hot melt adhesive.
It is essential to clean and thoroughly dry the surfaces intended for bonding before applying PUR hot melt adhesive. Proper surface preparation ensures optimal adhesion and bonding strength, preventing any potential issues such as poor adhesion or bond failure. By removing any contaminants or moisture from the surfaces, the hot melt adhesive can effectively create a strong and durable bond, enhancing the overall performance and longevity of the bonded materials.
Use the appropriate amount of hot melt adhesive to avoid excess or insufficient application.
When working with PUR hot melt adhesive, it is essential to use the appropriate amount to ensure optimal bonding performance. Applying an excess amount of adhesive can lead to wastage and potential bond failure due to uneven distribution or oozing. On the other hand, using insufficient adhesive may result in weak bonds that are prone to failure under stress. By carefully determining and applying the right amount of PUR hot melt adhesive, you can achieve strong, reliable bonds while maximizing efficiency and minimizing material waste.
Apply pressure to the bonded surfaces for proper adhesion of the hot melt adhesive.
To ensure the effective bonding of PUR hot melt adhesive, it is essential to apply pressure to the bonded surfaces. Applying pressure helps in achieving proper contact between the adhesive and the substrates, promoting strong adhesion. This step is crucial for creating a secure bond that can withstand various stresses and environmental conditions. Proper pressure application ensures that the adhesive spreads evenly, maximizing its bonding potential and enhancing the overall performance of the bonded assembly.
Allow sufficient time for the hot melt adhesive to cool and set after bonding.
It is essential to allow sufficient time for the hot melt adhesive to cool and set after bonding. This cooling and setting period is crucial for the adhesive to achieve its maximum bonding strength and durability. Rushing this process can compromise the integrity of the bond and lead to potential failure. By patiently allowing the hot melt adhesive to cool and set properly, you ensure a strong and long-lasting bond that meets the performance requirements of your application.
Store hot melt adhesives in a cool, dry place away from direct sunlight and heat sources.
It is essential to store PUR hot melt adhesives in a cool, dry place away from direct sunlight and heat sources to maintain their quality and performance. Exposure to high temperatures can cause the adhesive to degrade, leading to potential issues such as reduced bonding strength and consistency. By storing PUR hot melt adhesives properly, you can ensure that they remain effective and reliable for your bonding applications, ultimately contributing to the overall efficiency and quality of your production processes.
Regularly maintain your hot melt equipment to ensure consistent performance.
Regular maintenance of your hot melt equipment is essential to ensure consistent performance when using PUR hot melt adhesives. By regularly inspecting and servicing your equipment, you can prevent issues such as clogs, leaks, or uneven adhesive application that may affect the quality of your bonding. Proper maintenance not only prolongs the lifespan of your equipment but also helps in maintaining the efficiency and effectiveness of your production processes. Remember, a well-maintained hot melt system is key to achieving reliable and high-quality bonding results in your applications.