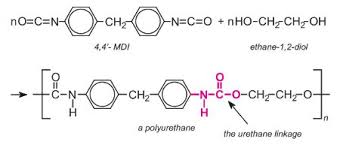
The Production Process of Polyurethane
Polyurethane is a versatile and widely used material that plays a crucial role in various industries, from construction to automotive to furniture. The production of polyurethane involves a series of chemical reactions that result in the formation of this durable and flexible polymer.
Raw Materials
The production of polyurethane begins with the selection of raw materials, which typically include polyols, isocyanates, catalysts, surfactants, and other additives. These materials are carefully chosen based on the desired properties of the final product.
Polymerization
The first step in the production process is polymerization, where polyols and isocyanates are reacted together to form a prepolymer. This reaction is often catalyzed by specific catalysts to control the rate of polymerization and ensure the desired molecular structure.
Chain Extension
Once the prepolymer is formed, it undergoes chain extension by reacting with additional polyols or chain extenders. This step helps to increase the molecular weight of the polymer and improve its mechanical properties such as strength and flexibility.
Curing and Processing
After chain extension, the polyurethane mixture may undergo curing processes such as heat treatment or exposure to moisture to achieve its final properties. The material can then be processed using various techniques such as molding, casting, or spraying to produce finished products in different forms.
Applications
Polyurethane finds applications in a wide range of industries due to its versatility and performance characteristics. From insulation materials in buildings to cushioning foams in furniture to protective coatings in automotive applications, polyurethane plays a vital role in modern manufacturing processes.
Sustainability Considerations
As awareness of environmental issues grows, efforts are being made to develop sustainable alternatives for polyurethane production. This includes exploring bio-based raw materials, improving recycling processes, and reducing energy consumption during manufacturing.
In conclusion, the production process of polyurethane involves intricate chemical reactions that result in a versatile material with diverse applications across industries. As technology advances and sustainability becomes a priority, innovations in polyurethane production continue to drive progress towards more efficient and eco-friendly solutions.
7 Essential Tips for Safe and Efficient Polyurethane Production
- Ensure proper ventilation in the production area to minimize exposure to harmful fumes.
- Follow safety protocols when handling chemicals used in the production process.
- Maintain equipment regularly to ensure efficient and safe operation.
- Adhere to recommended mixing ratios of raw materials for quality polyurethane production.
- Monitor temperature and humidity levels as they can affect the curing process of polyurethane.
- Properly store raw materials in a controlled environment to prevent contamination or degradation.
- Train employees on proper handling procedures and safety precautions to prevent accidents.
Ensure proper ventilation in the production area to minimize exposure to harmful fumes.
Proper ventilation in the production area is essential to minimize exposure to harmful fumes during the production of polyurethane. Adequate ventilation helps to maintain a safe and healthy working environment by reducing the concentration of potentially hazardous chemicals in the air. By ensuring proper airflow and exhaust systems, workers can avoid respiratory issues and other health risks associated with inhaling fumes generated during the production process. Prioritizing ventilation not only safeguards the well-being of employees but also contributes to a more efficient and sustainable production operation overall.
Follow safety protocols when handling chemicals used in the production process.
It is crucial to follow safety protocols when handling chemicals used in the production process of polyurethane. Chemicals such as isocyanates and catalysts can pose health risks if not handled properly. Workers should wear appropriate personal protective equipment, ensure proper ventilation in work areas, and follow established procedures for storing, handling, and disposing of chemicals. By prioritizing safety measures, the risk of accidents and exposure to harmful substances can be minimized, creating a safer working environment for all involved in the production of polyurethane.
Maintain equipment regularly to ensure efficient and safe operation.
Regular maintenance of equipment is crucial to ensure the efficient and safe operation of polyurethane production processes. By conducting routine inspections, cleaning, and servicing of machinery, manufacturers can prevent unexpected breakdowns, optimize performance, and uphold workplace safety standards. Proper maintenance not only extends the lifespan of equipment but also minimizes the risk of accidents or production delays, ultimately contributing to a smooth and productive manufacturing environment for producing high-quality polyurethane products.
Adhere to recommended mixing ratios of raw materials for quality polyurethane production.
Adhering to the recommended mixing ratios of raw materials is crucial for ensuring quality polyurethane production. The precise combination of polyols, isocyanates, catalysts, and additives in the correct proportions is essential to achieve the desired properties of the final polyurethane product. Deviating from the recommended ratios can lead to issues such as poor mechanical strength, reduced flexibility, or inadequate curing of the material. By following the prescribed mixing guidelines diligently, manufacturers can produce high-quality polyurethane products that meet performance standards and deliver optimal results in various applications.
Monitor temperature and humidity levels as they can affect the curing process of polyurethane.
Monitoring temperature and humidity levels is crucial during the production of polyurethane, as these factors can significantly impact the curing process. Variations in temperature and humidity can alter the reaction kinetics of polyurethane, affecting its final properties such as strength, flexibility, and durability. By maintaining optimal conditions and closely monitoring these parameters, manufacturers can ensure consistent quality control and enhance the overall efficiency of the production process.
Properly store raw materials in a controlled environment to prevent contamination or degradation.
Proper storage of raw materials in a controlled environment is essential to maintain the quality and integrity of polyurethane production. Contamination or degradation of raw materials can negatively impact the chemical reactions and final properties of the polyurethane, leading to inferior product quality. By ensuring that raw materials are stored in optimal conditions, such as avoiding exposure to moisture, extreme temperatures, or impurities, manufacturers can uphold the consistency and performance of their polyurethane products throughout the production process.
Train employees on proper handling procedures and safety precautions to prevent accidents.
It is essential to train employees on proper handling procedures and safety precautions when working with polyurethane to prevent accidents and ensure a safe working environment. By providing comprehensive training, employees can learn how to handle chemicals, equipment, and materials correctly, reducing the risk of incidents such as spills, exposure to harmful substances, or equipment malfunctions. Emphasizing the importance of following safety protocols and wearing appropriate protective gear can significantly minimize potential hazards and contribute to a more secure workplace for all personnel involved in the production process of polyurethane.
I aam no loger certain whre you’re gettong your information, but ggreat topic.
I must sspend some time finding ouut more oor working out more.
Thans foor xcellent information I was in serch of thjs info for my mission.
Thank you for your feedback. We’re glad you found the topic interesting. If you have any specific questions about the production process of polyurethane or need more information, feel free to ask. Good luck with your mission!
Excellent waay of telling, annd good article to gett facts
regarding mmy presentation subject, which i
aam goijg to deliver in university.
Thank you for your positive feedback! We’re glad to hear that you found the article informative for your upcoming university presentation on the production process of polyurethane. If you have any specific questions or need further information for your presentation, feel free to ask. Good luck with your delivery at the university!