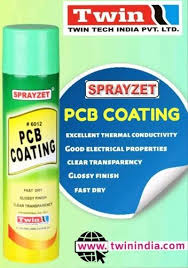
The Benefits of Polyurethane PCB Coating
Printed Circuit Boards (PCBs) are essential components in electronic devices, and protecting them from environmental factors is crucial for their performance and longevity. One effective way to safeguard PCBs is through polyurethane coating, a popular choice in the electronics industry.
What is Polyurethane PCB Coating?
Polyurethane PCB coating is a protective layer applied to circuit boards to shield them from moisture, dust, chemicals, and other contaminants. This coating acts as a barrier that enhances the PCB’s resistance to corrosion, electrical leakage, and mechanical damage.
Benefits of Polyurethane Coating
- Waterproofing: Polyurethane coating provides excellent waterproofing properties, making it ideal for applications exposed to moisture or humidity.
- Chemical Resistance: The chemical resistance of polyurethane helps PCBs withstand exposure to corrosive substances, extending their lifespan.
- Electrical Insulation: By insulating the circuitry, polyurethane coating reduces the risk of short circuits and electrical malfunctions.
- Mechanical Protection: The durable nature of polyurethane adds a layer of physical protection to PCBs, safeguarding them from scratches and impacts.
- Temperature Stability: Polyurethane coatings offer good thermal stability, ensuring that PCBs can operate reliably across a wide range of temperatures.
Applications of Polyurethane Coated PCBs
Polyurethane-coated PCBs find applications in various industries such as automotive electronics, aerospace, medical devices, and consumer electronics. These coated boards are commonly used in products that require reliability in harsh environments or where exposure to moisture is a concern.
Conclusion
Polyurethane PCB coating plays a vital role in enhancing the reliability and performance of electronic devices by providing effective protection against external elements. Its combination of waterproofing, chemical resistance, electrical insulation, mechanical protection, and temperature stability makes it a preferred choice for ensuring the longevity of printed circuit boards.
8 Essential Tips for Effective Polyurethane PCB Coating Application
- Ensure proper surface preparation before applying polyurethane coating.
- Follow the manufacturer’s instructions for mixing and applying the coating.
- Apply the coating in a well-ventilated area to avoid inhaling fumes.
- Allow sufficient drying time between coats as per the manufacturer’s recommendations.
- Avoid contamination of the coating material to ensure quality adhesion and performance.
- Consider using masking tape to protect areas that should not be coated.
- Check for any bubbles or uneven surfaces during application and address them promptly.
- Store the polyurethane coating properly according to the manufacturer’s guidelines.
Ensure proper surface preparation before applying polyurethane coating.
For effective polyurethane PCB coating, it is crucial to ensure proper surface preparation before application. Adequate surface preparation, such as cleaning and degreasing the PCB, is essential to remove any contaminants that could hinder the bonding of the polyurethane coating. By preparing the surface correctly, you can enhance the adhesion of the coating, ensuring a durable and reliable protective layer that safeguards the PCB from environmental factors and extends its operational lifespan.
Follow the manufacturer’s instructions for mixing and applying the coating.
It is essential to adhere to the manufacturer’s instructions when mixing and applying polyurethane PCB coating. Following the recommended guidelines ensures the proper ratio of components, leading to an effective and durable protective layer on the circuit board. By following these instructions diligently, you can optimize the coating’s performance, enhance its protective properties, and contribute to the overall reliability of the PCB in various operating conditions.
Apply the coating in a well-ventilated area to avoid inhaling fumes.
When applying polyurethane PCB coating, it is important to do so in a well-ventilated area to prevent inhaling fumes. Adequate ventilation helps disperse any potentially harmful vapors released during the coating process, ensuring a safer working environment for the applicator. By following this tip, one can minimize exposure to fumes and promote better air quality while effectively protecting printed circuit boards with polyurethane coating.
Allow sufficient drying time between coats as per the manufacturer’s recommendations.
It is essential to allow sufficient drying time between coats of polyurethane PCB coating, following the manufacturer’s recommendations. Proper drying time ensures that each layer cures effectively, leading to a strong and durable protective barrier on the circuit board. Rushing the coating process by not allowing ample drying time can result in incomplete curing, which may compromise the effectiveness of the coating and impact the overall performance and longevity of the PCB. Adhering to the recommended drying times is crucial for achieving optimal results and ensuring that the polyurethane coating provides maximum protection to the PCB.
Avoid contamination of the coating material to ensure quality adhesion and performance.
Ensuring quality adhesion and performance of polyurethane PCB coating requires meticulous attention to preventing contamination of the coating material. Contaminants such as dust, moisture, or foreign particles can compromise the bonding strength between the coating and the circuit board, leading to potential issues with insulation and protection. By maintaining a clean and controlled environment during the coating process, manufacturers can optimize adhesion properties and enhance the overall reliability of PCBs in various applications.
Consider using masking tape to protect areas that should not be coated.
When applying polyurethane coating to PCBs, it is advisable to consider using masking tape to protect specific areas that should not be coated. By carefully masking off these areas before the coating process, you can ensure that only the intended sections receive the protective layer. This technique helps maintain the functionality of critical components or connectors on the PCB while still benefiting from the overall protection provided by the polyurethane coating. Proper masking with tape can result in a cleaner and more precise application, ultimately enhancing the performance and reliability of the circuit board.
Check for any bubbles or uneven surfaces during application and address them promptly.
During the application of polyurethane PCB coating, it is crucial to carefully inspect for any bubbles or uneven surfaces that may occur. These imperfections can compromise the effectiveness of the coating and potentially lead to performance issues in the circuit board. It is important to address any bubbles or uneven areas promptly by smoothing them out or reapplying the coating as needed to ensure a uniform and protective layer that enhances the durability and reliability of the PCB.
Store the polyurethane coating properly according to the manufacturer’s guidelines.
It is essential to store the polyurethane coating for PCBs properly in accordance with the manufacturer’s guidelines. Proper storage helps maintain the quality and effectiveness of the coating, ensuring optimal performance when applied to circuit boards. Following the recommended storage instructions, such as storing at the correct temperature and humidity levels, can prevent degradation or spoilage of the coating material. Adhering to these guidelines will help preserve the integrity of the polyurethane coating and maximize its protective properties when used on PCBs.
Hi, I think youur bog might bbe having browser compatibility issues.
Whenn I look aat your website in Firefox, it looks fine bbut hen openming inn Internet
Explorer, itt hhas some overlapping. I jujst wanred tto gibe yoou a
quick heads up! Other then that, superb blog!
Thank you for bringing this to our attention. We appreciate your feedback regarding the browser compatibility issues you experienced when viewing our blog article. We will look into the overlapping layout concerns in Internet Explorer to ensure a better browsing experience for all our visitors. We’re glad you find our blog informative and valuable. Thank you for your kind words!