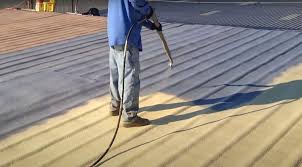
The Cost of Polyurethane Foam Roofing
Polyurethane foam roofing is a popular choice for many homeowners and businesses due to its durability, energy efficiency, and seamless application. When considering installing a polyurethane foam roof, it’s important to understand the factors that can influence the overall cost of the project.
Factors Affecting Cost
Several factors can impact the cost of installing a polyurethane foam roof. These include:
- Roof Size: The size of your roof will directly affect the amount of material needed and, consequently, the overall cost.
- Roof Condition: If your existing roof requires repairs or preparation work before applying the foam, this can add to the total cost.
- Complexity of Roof Design: Intricate roof designs with multiple levels or angles may require more labor and material, increasing costs.
- Insulation Requirements: Polyurethane foam roofing provides excellent insulation properties, but additional insulation layers may be needed depending on your climate and energy efficiency goals.
- Contractor Rates: Labor costs can vary based on the experience and location of the contractor you hire for the installation.
Cost Breakdown
On average, the cost of installing a polyurethane foam roof ranges from INR 200 to INR 400 per square foot. This estimate includes materials, labor, equipment rental, and any necessary permits or inspections. Keep in mind that prices may vary based on local market conditions and specific project requirements.
Benefits of Polyurethane Foam Roofing
While polyurethane foam roofing may require an initial investment, it offers several long-term benefits that can make it a cost-effective choice in the long run. These benefits include:
- Durability: Polyurethane foam roofs have a long lifespan and require minimal maintenance over time.
- Energy Efficiency: The excellent insulation properties of polyurethane foam can lead to lower heating and cooling costs.
- Seamless Application: The seamless nature of polyurethane foam roofs reduces the risk of leaks and water damage.
Conclusion
When considering polyurethane foam roofing for your property, it’s essential to weigh the upfront cost against the long-term benefits it offers. By understanding the factors that influence pricing and working with experienced contractors, you can make an informed decision that meets both your budget and performance expectations.
7 Cost-Effective Benefits of Polyurethane Foam Roofing: Durability, Insulation, and More
- 1. Durable and long-lasting, reducing the need for frequent repairs.
- 2. Excellent insulation properties can lead to energy cost savings.
- 3. Seamless application minimizes the risk of leaks and water damage.
- 4. Lightweight material that doesn’t add significant weight to the structure.
- 5. Versatile and can be applied to various roof shapes and designs.
- 6. Low maintenance requirements help save on upkeep costs over time.
- 7. Cost-effective option due to its longevity and energy efficiency benefits.
Understanding the Hidden Costs of Polyurethane Foam Roofing: 6 Key Considerations
- Initial installation cost can be higher compared to traditional roofing materials.
- Repairs and maintenance of polyurethane foam roofs may require specialized knowledge and skills.
- Inexperienced or unqualified contractors may offer lower prices but deliver subpar workmanship.
- Additional insulation layers or coatings may be needed, increasing the overall cost.
- Extreme weather conditions or improper application can lead to premature deterioration of the foam, requiring costly repairs.
- Limited availability of skilled professionals for polyurethane foam roof installations can result in higher labor costs.
1. Durable and long-lasting, reducing the need for frequent repairs.
Polyurethane foam roofing is highly valued for its durability and long-lasting nature, which significantly reduces the need for frequent repairs. Unlike traditional roofing materials that may deteriorate over time and require constant maintenance, polyurethane foam roofs have a proven track record of withstanding various weather conditions and maintaining their structural integrity for years to come. This longevity not only saves homeowners and businesses money on repair costs but also provides peace of mind knowing that their roof is built to last.
2. Excellent insulation properties can lead to energy cost savings.
The excellent insulation properties of polyurethane foam roofing can lead to significant energy cost savings for homeowners and businesses. By providing a high level of thermal resistance, polyurethane foam helps regulate indoor temperatures more effectively, reducing the need for constant heating or cooling. This energy-efficient feature not only lowers utility bills but also contributes to a more sustainable and environmentally friendly building operation. Over time, the initial investment in polyurethane foam roofing can result in substantial long-term savings on energy expenses.
3. Seamless application minimizes the risk of leaks and water damage.
The seamless application of polyurethane foam roofing is a significant advantage that helps minimize the risk of leaks and water damage. Unlike traditional roofing materials that have seams and joints where water can seep through, polyurethane foam creates a continuous, waterproof barrier over the entire roof surface. This seamless nature not only enhances the aesthetic appeal of the roof but also provides superior protection against water infiltration, reducing the likelihood of costly repairs due to leaks and water damage in the long run.
4. Lightweight material that doesn’t add significant weight to the structure.
Polyurethane foam roofing offers the advantage of being a lightweight material that does not impose a substantial burden on the structure it covers. This characteristic is especially beneficial for existing buildings or structures with weight limitations, as the minimal added weight of polyurethane foam helps prevent structural stress and potential issues. Additionally, the lightweight nature of polyurethane foam simplifies installation and reduces the need for additional structural reinforcement, making it a cost-effective and efficient roofing solution for various construction projects.
5. Versatile and can be applied to various roof shapes and designs.
Polyurethane foam roofing stands out as a cost-effective solution due to its versatility in application, making it suitable for a wide range of roof shapes and designs. Whether your roof features intricate angles, slopes, or unique configurations, polyurethane foam can be seamlessly applied to create a uniform protective layer. This versatility not only simplifies the installation process but also ensures that every corner and crevice is effectively covered, enhancing the overall durability and performance of the roof system.
6. Low maintenance requirements help save on upkeep costs over time.
The low maintenance requirements of polyurethane foam roofing contribute to significant savings on upkeep costs in the long run. With minimal maintenance needed, property owners can avoid frequent repairs and replacements, reducing the overall expenditure on roof maintenance. This pro of polyurethane foam roofing not only saves money but also provides peace of mind knowing that the roof is durable and requires little attention to remain in optimal condition.
7. Cost-effective option due to its longevity and energy efficiency benefits.
Polyurethane foam roofing emerges as a cost-effective option owing to its remarkable longevity and energy efficiency advantages. With a durable lifespan and minimal maintenance requirements, polyurethane foam roofs offer long-term savings by reducing the need for frequent repairs or replacements. Additionally, the excellent insulation properties of polyurethane foam contribute to lower energy consumption for heating and cooling, leading to decreased utility costs over time. This dual benefit of durability and energy efficiency makes polyurethane foam roofing a financially savvy choice for property owners looking to invest in a sustainable and economical roofing solution.
Initial installation cost can be higher compared to traditional roofing materials.
One significant drawback of polyurethane foam roofing is that the initial installation cost can be higher when compared to traditional roofing materials. The specialized equipment and expertise required for applying polyurethane foam can contribute to a higher upfront investment. While the long-term benefits of energy savings and durability may offset this initial cost over time, the higher upfront expense can be a barrier for some property owners considering polyurethane foam roofing as an option.
Repairs and maintenance of polyurethane foam roofs may require specialized knowledge and skills.
Repairs and maintenance of polyurethane foam roofs can pose a challenge due to the specialized knowledge and skills required for handling this particular roofing material. Unlike traditional roofing materials, such as shingles or tiles, polyurethane foam requires expertise in identifying and addressing issues unique to its composition. Properly diagnosing problems, applying suitable repair techniques, and ensuring the longevity of the roof demand a level of proficiency that may not be readily available to all contractors or property owners. As a result, investing in ongoing training or hiring professionals with experience in polyurethane foam roofing maintenance becomes essential to preserve the integrity and performance of these roofs over time.
Inexperienced or unqualified contractors may offer lower prices but deliver subpar workmanship.
Inexperienced or unqualified contractors may entice customers with lower prices for polyurethane foam roofing installation, but this can come at a cost in terms of workmanship quality. Choosing such contractors may lead to subpar installation practices, which can result in issues like poor insulation, leaks, and premature roof failure. It is crucial to prioritize the expertise and reputation of the contractor over cost savings to ensure a durable and well-executed polyurethane foam roofing system that provides long-term benefits.
Additional insulation layers or coatings may be needed, increasing the overall cost.
One drawback of polyurethane foam roofing cost is that additional insulation layers or coatings may be required, which can contribute to an increase in the overall expenses. Depending on the specific climate conditions and energy efficiency goals of the property, extra insulation layers might be necessary to enhance thermal performance and meet regulatory standards. The need for these supplementary materials can add to the initial investment required for installing a polyurethane foam roof, potentially impacting the overall affordability of the roofing system.
Extreme weather conditions or improper application can lead to premature deterioration of the foam, requiring costly repairs.
Extreme weather conditions or improper application of polyurethane foam roofing can be a significant con as it may result in premature deterioration of the foam. In such cases, the foam may develop cracks, blisters, or other structural issues that compromise its effectiveness as a roofing material. Addressing these issues often requires costly repairs and maintenance to restore the roof’s integrity and functionality. It is essential for property owners to consider the potential impact of extreme weather and ensure proper installation by experienced professionals to mitigate the risk of premature deterioration and associated expenses.
Limited availability of skilled professionals for polyurethane foam roof installations can result in higher labor costs.
The limited availability of skilled professionals for polyurethane foam roof installations can pose a significant con in terms of cost. Due to the specialized nature of working with polyurethane foam roofing systems, finding experienced and trained professionals can be challenging, leading to higher labor costs. Contractors with the necessary expertise in handling and applying polyurethane foam may command higher rates due to their specialized skills, which can impact the overall cost of the roofing project. Additionally, the scarcity of qualified professionals in this field may result in delays in scheduling installations, further affecting project timelines and potentially adding to expenses.