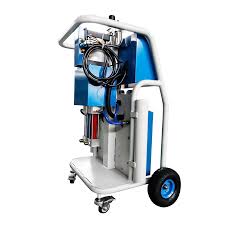
The Advantages of Polyurethane Foam Injection Molding
Polyurethane foam injection molding is a versatile manufacturing process that offers numerous benefits across various industries. This innovative technique involves injecting liquid polyurethane into a mold cavity, where it expands and solidifies to create a wide range of products with unique properties.
Key Advantages:
- Lightweight: Polyurethane foam is known for its lightweight nature, making it ideal for applications where weight reduction is crucial.
- Durability: Products manufactured through foam injection molding are durable and resistant to wear and tear, ensuring long-lasting performance.
- Customization: The flexibility of polyurethane foam allows for easy customization of products to meet specific design requirements.
- Insulation Properties: Polyurethane foam offers excellent insulation properties, making it suitable for use in thermal and acoustic insulation applications.
- Cost-Effective Production: The efficiency of the injection molding process results in cost-effective production with reduced material waste.
Applications:
Polyurethane foam injection molding finds applications in a wide range of industries, including automotive, furniture, construction, and packaging. Common products produced using this method include automotive interior components, furniture cushions, insulation panels, and protective packaging materials.
Environmental Considerations:
In addition to its performance benefits, polyurethane foam injection molding can also contribute to sustainability efforts. By optimizing material usage and energy efficiency during production, manufacturers can reduce their environmental footprint while delivering high-quality products.
In Conclusion
The versatility, durability, and cost-effectiveness of polyurethane foam injection molding make it a preferred choice for manufacturers looking to create innovative products with exceptional properties. With its wide range of applications and environmental advantages, this manufacturing process continues to drive advancements across various industries.
Top 9 Advantages of Polyurethane Foam Injection Molding
- Lightweight nature of polyurethane foam
- Durability and resistance to wear and tear
- Easy customization to meet specific design requirements
- Excellent insulation properties for thermal and acoustic applications
- Cost-effective production with reduced material waste
- Versatile applications across multiple industries
- Enhanced energy efficiency during manufacturing process
- Ability to create complex shapes and intricate designs
- Contribution to sustainability efforts through optimized material usage
Challenges in Polyurethane Foam Injection Molding: Material Limitations, High Setup Costs, Complex Tooling, and Quality Control Issues
- Limited material options compared to other molding processes.
- Initial setup costs can be relatively high, especially for small-scale production.
- Complex molds may require longer lead times and higher tooling costs.
- Foam expansion control can be challenging, leading to potential quality issues in final products.
Lightweight nature of polyurethane foam
The lightweight nature of polyurethane foam in injection molding offers a significant advantage, especially in industries where weight reduction is a key consideration. Products manufactured using polyurethane foam are inherently lighter compared to traditional materials, making them ideal for applications where weight plays a crucial role. This characteristic not only enhances the ease of handling and transportation but also contributes to overall energy efficiency and cost-effectiveness in various manufacturing processes.
Durability and resistance to wear and tear
Polyurethane foam injection molding stands out for its exceptional durability and resistance to wear and tear. Products manufactured through this process exhibit robustness and longevity, making them ideal for applications where reliability is paramount. Whether used in automotive components, furniture cushions, insulation panels, or packaging materials, the inherent strength of polyurethane foam ensures that the products can withstand daily use and environmental factors without compromising their integrity. This pro of durability and resistance to wear and tear makes polyurethane foam injection molding a preferred choice for industries seeking long-lasting and high-performance solutions.
Easy customization to meet specific design requirements
Polyurethane foam injection molding stands out for its pro of easy customization to meet specific design requirements. This feature allows manufacturers to tailor products according to precise specifications, making it a preferred choice for industries that require unique shapes, sizes, or properties in their end products. Whether it’s creating intricate designs, adjusting material densities, or incorporating special features, the flexibility of polyurethane foam injection molding enables manufacturers to deliver highly customized solutions that meet the exact needs of their customers.
Excellent insulation properties for thermal and acoustic applications
Polyurethane foam injection molding offers excellent insulation properties for thermal and acoustic applications. The unique composition of polyurethane foam allows it to effectively regulate temperature and sound transmission, making it an ideal choice for products requiring insulation against heat, cold, or noise. Whether used in construction for energy-efficient buildings, in automotive interiors for noise reduction, or in packaging materials for thermal protection, the superior insulation capabilities of polyurethane foam contribute to enhanced comfort, efficiency, and performance across a wide range of applications.
Cost-effective production with reduced material waste
Polyurethane foam injection molding offers a significant advantage in cost-effective production by minimizing material waste. This efficiency in material usage not only helps manufacturers save on costs but also contributes to sustainable practices by reducing environmental impact. By utilizing only the necessary amount of polyurethane material required for each product, this manufacturing process optimizes resources and promotes economic viability while maintaining high-quality standards in production.
Versatile applications across multiple industries
Polyurethane foam injection molding stands out for its versatility in applications across multiple industries. From automotive components to furniture cushions, insulation panels to packaging materials, polyurethane foam offers a wide range of uses due to its ability to be customized for specific design requirements. This versatility makes it a preferred choice for manufacturers looking to create innovative products that meet diverse industry needs efficiently and effectively.
Enhanced energy efficiency during manufacturing process
Polyurethane foam injection molding offers the significant advantage of enhanced energy efficiency during the manufacturing process. This is achieved through the optimized use of energy resources required for heating, mixing, and injecting the liquid polyurethane into molds. By reducing energy consumption in production, manufacturers can lower operational costs and minimize their environmental impact. This pro not only contributes to sustainable manufacturing practices but also underscores the cost-effectiveness of polyurethane foam injection molding as a preferred method for creating high-quality products with minimal energy waste.
Ability to create complex shapes and intricate designs
Polyurethane foam injection molding stands out for its remarkable ability to create complex shapes and intricate designs with precision and consistency. This pro of the manufacturing process enables designers and engineers to bring their most creative and innovative ideas to life, pushing the boundaries of product development. Whether it’s intricate patterns, detailed textures, or unique geometries, polyurethane foam injection molding offers unparalleled flexibility in producing components that meet the most demanding design requirements across various industries.
Contribution to sustainability efforts through optimized material usage
Polyurethane foam injection molding contributes significantly to sustainability efforts by optimizing material usage. This innovative manufacturing process minimizes waste and maximizes efficiency, ensuring that resources are utilized effectively. By reducing material consumption and improving production yields, polyurethane foam injection molding helps manufacturers lower their environmental impact and operate in a more sustainable manner. This focus on optimized material usage not only benefits the environment but also supports cost-effective production practices, making it a win-win solution for both businesses and the planet.
Limited material options compared to other molding processes.
Polyurethane foam injection molding, despite its many advantages, faces a limitation in terms of material options when compared to other molding processes. The range of materials that can be used in polyurethane foam injection molding is somewhat limited, which may restrict the design possibilities for certain applications. This constraint can pose challenges for manufacturers seeking specific material properties or characteristics that may not be readily available within the scope of polyurethane foam molding. As a result, careful consideration and evaluation of material requirements are essential when opting for polyurethane foam injection molding to ensure that the chosen material aligns with the desired product specifications and performance criteria.
Initial setup costs can be relatively high, especially for small-scale production.
One significant drawback of polyurethane foam injection molding is the relatively high initial setup costs, particularly for small-scale production operations. The investment required for specialized equipment, molds, and training can pose a financial challenge for smaller businesses or startups looking to adopt this manufacturing process. These upfront expenses can deter companies with limited resources from leveraging the benefits of polyurethane foam injection molding, potentially limiting their ability to compete in the market effectively.
Complex molds may require longer lead times and higher tooling costs.
Complex molds used in polyurethane foam injection molding processes may pose a significant challenge due to longer lead times and higher tooling costs. The intricate designs and detailed features of these molds demand meticulous planning and precision, leading to extended production timelines. Additionally, the complexity of the molds necessitates advanced tooling techniques and materials, resulting in increased manufacturing expenses. Despite these drawbacks, careful consideration and strategic planning can help mitigate the impact of these factors on overall production efficiency and cost-effectiveness.
Foam expansion control can be challenging, leading to potential quality issues in final products.
Controlling foam expansion in polyurethane foam injection molding can pose a significant challenge, potentially resulting in quality issues in the final products. The unpredictable nature of foam expansion during the molding process can lead to variations in product dimensions and densities, impacting the overall quality and consistency of the end products. Manufacturers must carefully monitor and adjust various parameters, such as temperature, pressure, and chemical composition, to ensure proper foam expansion control and minimize defects in the finished components. Failure to address this con effectively can result in substandard products that do not meet the required specifications for performance and durability.