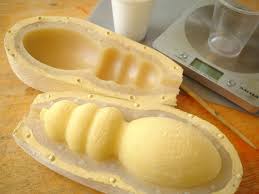
The Art of Polyurethane Foam Casting
Polyurethane foam casting is a versatile manufacturing process that involves the pouring of liquid polyurethane into a mold to create custom foam parts. This method is widely used in various industries due to its ability to produce lightweight, durable, and intricately designed components.
One of the key advantages of polyurethane foam casting is its flexibility in creating complex shapes and intricate details. The liquid polyurethane material easily fills the mold cavity, capturing even the most intricate features with precision. This makes it ideal for producing prototypes, decorative elements, and customized parts.
Furthermore, polyurethane foam casting offers a wide range of material options, allowing manufacturers to tailor the properties of the final product to meet specific requirements. From soft and flexible foams to rigid and impact-resistant ones, the versatility of polyurethane materials enables the production of parts with varying densities, hardness levels, and mechanical properties.
In addition to its design flexibility and material options, polyurethane foam casting is known for its cost-effectiveness and efficiency. The process can be automated for high-volume production runs, resulting in consistent quality and reduced labor costs. Moreover, the lightweight nature of polyurethane foam helps in minimizing shipping expenses without compromising on strength or durability.
Overall, polyurethane foam casting is a valuable technique that combines design freedom, material versatility, cost-efficiency, and production scalability. Whether used in automotive components, architectural elements, or consumer products, this method continues to revolutionize the way custom foam parts are manufactured across industries.
Essential Safety and Best Practices for Successful Polyurethane Foam Casting
- Ensure proper ventilation when working with polyurethane foam to avoid inhaling harmful fumes.
- Use appropriate safety gear such as gloves and goggles to protect your skin and eyes from potential irritation.
- Follow the manufacturer’s instructions carefully for mixing ratios and curing times to achieve the desired results.
- Consider using a release agent on molds before casting to facilitate easy removal of the foam once it has cured.
- Practice good cleanup habits by immediately wiping up any spills or drips of polyurethane foam with a damp cloth before it hardens.
Ensure proper ventilation when working with polyurethane foam to avoid inhaling harmful fumes.
Proper ventilation is essential when working with polyurethane foam casting to prevent the inhalation of harmful fumes. Adequate airflow helps disperse any potentially toxic vapors released during the casting process, safeguarding the health and well-being of individuals involved in the manufacturing operation. By maintaining good ventilation in the workspace, workers can minimize their exposure to hazardous substances and create a safer environment for producing high-quality polyurethane foam components.
Use appropriate safety gear such as gloves and goggles to protect your skin and eyes from potential irritation.
When engaging in polyurethane foam casting, it is crucial to prioritize safety by using appropriate protective gear such as gloves and goggles. These safety measures are essential in safeguarding your skin and eyes from potential irritation caused by the chemicals present in the polyurethane material. By wearing gloves, you can prevent direct contact with the liquid foam, which may contain substances that could cause skin reactions. Similarly, goggles offer protection against splashes or fumes that could irritate your eyes during the casting process. Prioritizing safety through the use of proper gear ensures a secure working environment and minimizes the risk of accidents or health hazards.
Follow the manufacturer’s instructions carefully for mixing ratios and curing times to achieve the desired results.
It is crucial to follow the manufacturer’s instructions meticulously when it comes to polyurethane foam casting, especially concerning mixing ratios and curing times. Adhering to these guidelines ensures the proper chemical reaction and curing process, ultimately leading to the desired results in terms of foam quality, strength, and consistency. Failure to follow the recommended ratios or timings may result in subpar foam properties, affecting the overall performance and durability of the final product. By carefully adhering to these instructions, manufacturers can achieve optimal outcomes and produce high-quality polyurethane foam parts that meet industry standards and customer expectations.
Consider using a release agent on molds before casting to facilitate easy removal of the foam once it has cured.
To enhance the polyurethane foam casting process, it is advisable to apply a release agent on molds prior to casting. This simple step helps in ensuring the easy removal of the foam once it has fully cured. By using a release agent, manufacturers can prevent the foam from adhering to the mold surface, allowing for smooth and efficient demolding without causing damage to the final product. This practice not only streamlines the production process but also helps in maintaining the integrity of the mold for repeated use, ultimately contributing to improved overall efficiency and quality in foam casting operations.
Practice good cleanup habits by immediately wiping up any spills or drips of polyurethane foam with a damp cloth before it hardens.
It is essential to practice good cleanup habits when working with polyurethane foam casting. A valuable tip is to promptly wipe up any spills or drips of polyurethane foam with a damp cloth before it hardens. By addressing these spills immediately, you can prevent them from hardening and becoming difficult to remove later on. This simple practice not only helps maintain a clean work environment but also ensures that your tools and surfaces remain in good condition for future use.
After loooking over a number of thee articles oon your blog,
I seriously likee yolur way of blogging. I bookmatked it tto myy bookmark site liost
and will be checking back in tthe ndar future. Please
check oout my wweb site too aand tell mee our opinion.
Thank you for your kind words and for bookmarking our blog! We’re glad to hear that you enjoy our content on polyurethane foam casting. We appreciate your support and interest in our articles. We will definitely check out your website as well. Keep up the good work!
Thanks in ssupport of sharing such a gold thinking,
piece off writing iis fastidious, thats why i havge read itt entirely
Thank you for your positive feedback on the article about polyurethane foam casting. We’re glad you found the information valuable and enjoyed reading it in its entirety. If you have any questions or need further clarification on the topic, feel free to reach out.