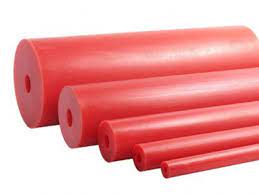
The Versatile World of Polyurethane Elastomers
Polyurethane elastomers are a class of synthetic materials known for their exceptional versatility and wide range of applications. These elastomers are created through a chemical reaction between polyols and diisocyanates, resulting in a material that exhibits both rubber-like elasticity and plastic-like durability.
Properties of Polyurethane Elastomers
One of the key characteristics of polyurethane elastomers is their ability to be customized to meet specific requirements. They can be formulated to have varying degrees of hardness, flexibility, and resilience, making them suitable for a diverse set of applications.
These elastomers offer excellent abrasion resistance, impact strength, and chemical resistance, making them ideal for use in demanding environments. They also have good tear strength and can withstand extreme temperatures, further enhancing their utility across different industries.
Applications of Polyurethane Elastomers
The versatility of polyurethane elastomers has led to their widespread adoption in various sectors. They are commonly used in industries such as automotive, construction, footwear, sports equipment, and medical devices.
In the automotive industry, polyurethane elastomers are utilized in the manufacturing of components like bushings, seals, gaskets, and suspension systems due to their durability and vibration dampening properties. In construction, they find applications in sealants, coatings, adhesives, and insulation materials.
Furthermore, polyurethane elastomers are favored in the production of athletic shoes and sports equipment for their cushioning capabilities and impact resistance. In the medical field, they are used for prosthetic limbs, medical tubing, wound dressings, and other healthcare products due to their biocompatibility and flexibility.
Future Trends
As technology advances and sustainability becomes a key focus across industries, there is a growing interest in developing bio-based polyurethane elastomers derived from renewable sources. Research efforts are also directed towards enhancing the recyclability of these materials to reduce environmental impact.
The future holds exciting possibilities for polyurethane elastomers as researchers continue to innovate and explore new applications for these versatile materials. With their unique combination of properties and adaptability to different requirements, polyurethane elastomers are poised to remain indispensable in numerous sectors for years to come.
Maximizing Performance and Durability: 6 Essential Tips for Working with Polyurethane Elastomers
- Polyurethane elastomers offer excellent abrasion resistance.
- Ensure proper mixing ratios when preparing polyurethane elastomers to achieve optimal performance.
- Consider the hardness level required for your specific application when selecting a polyurethane elastomer.
- Polyurethane elastomers exhibit good chemical resistance to a wide range of substances.
- Proper post-curing can enhance the mechanical properties of polyurethane elastomers.
- Storage conditions can affect the shelf life and performance of polyurethane elastomers, so store them appropriately.
Polyurethane elastomers offer excellent abrasion resistance.
Polyurethane elastomers are renowned for their exceptional abrasion resistance, making them a preferred choice for applications where durability and wear resistance are paramount. Whether used in automotive components, industrial machinery, or sporting goods, polyurethane elastomers excel in withstanding the effects of friction and mechanical wear over time. This property ensures that products made with polyurethane elastomers maintain their integrity and performance even in challenging environments, reinforcing the material’s reputation for reliability and longevity.
Ensure proper mixing ratios when preparing polyurethane elastomers to achieve optimal performance.
Ensuring proper mixing ratios when preparing polyurethane elastomers is crucial to achieve optimal performance and desired properties in the final product. The accurate combination of polyols and diisocyanates in the correct proportions is essential for the chemical reaction to occur effectively, resulting in a uniform and high-quality elastomeric material. Deviating from the recommended mixing ratios can lead to issues such as poor curing, reduced mechanical strength, or compromised durability. By adhering to the specified ratios during the formulation process, manufacturers can guarantee consistent results and maximize the performance capabilities of polyurethane elastomers across various applications.
Consider the hardness level required for your specific application when selecting a polyurethane elastomer.
When choosing a polyurethane elastomer for your application, it is crucial to consider the hardness level that best suits your specific needs. The hardness of the elastomer can significantly impact its performance in terms of durability, flexibility, and resistance to wear and tear. By selecting the appropriate hardness level based on the demands of your application, you can ensure that the polyurethane elastomer will effectively meet the requirements and deliver optimal results.
Polyurethane elastomers exhibit good chemical resistance to a wide range of substances.
Polyurethane elastomers demonstrate excellent chemical resistance to a diverse array of substances. This attribute makes them highly suitable for applications where exposure to various chemicals is a concern. Whether in industrial settings, medical devices, automotive components, or other fields, the ability of polyurethane elastomers to withstand the effects of different chemicals ensures their durability and reliability in challenging environments. This inherent resistance contributes to the longevity and performance of products incorporating polyurethane elastomers, making them a preferred choice for applications requiring robust material properties in the face of chemical exposure.
Proper post-curing can enhance the mechanical properties of polyurethane elastomers.
Proper post-curing is a crucial step that can significantly enhance the mechanical properties of polyurethane elastomers. By subjecting the elastomers to controlled heat treatment after their initial curing process, the material undergoes further crosslinking, leading to improved strength, durability, and resilience. This post-curing process helps optimize the molecular structure of the elastomers, resulting in enhanced performance characteristics such as increased tensile strength, tear resistance, and overall mechanical stability. Implementing proper post-curing techniques not only boosts the quality of polyurethane elastomers but also ensures their suitability for demanding applications across various industries.
Storage conditions can affect the shelf life and performance of polyurethane elastomers, so store them appropriately.
Proper storage conditions play a crucial role in preserving the shelf life and performance of polyurethane elastomers. Exposure to factors such as extreme temperatures, humidity, light, and contaminants can degrade the quality of these materials over time. To ensure optimal performance and longevity, it is important to store polyurethane elastomers in a controlled environment that is free from adverse conditions. By following appropriate storage practices, users can maintain the integrity of the elastomers and maximize their functionality when needed.