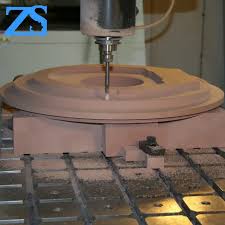
Machining Polyurethane Foam: Techniques and Considerations
Polyurethane foam is a versatile material used in various industries due to its lightweight nature, excellent cushioning properties, and thermal insulation capabilities. Machining polyurethane foam requires specialized techniques to achieve precise cuts and shapes. Here are some key considerations when machining polyurethane foam:
Cutting Tools
When machining polyurethane foam, it is essential to use sharp cutting tools that can provide clean cuts without causing excessive friction or heat buildup. Common cutting tools for machining polyurethane foam include band saws, CNC routers, water jets, and laser cutters.
Speed and Feed Rates
The speed and feed rates at which the cutting tool moves through the polyurethane foam are crucial factors that impact the quality of the machined parts. It is important to adjust the speed and feed rates based on the density and thickness of the foam to prevent tearing or deformation.
Dust Control
Machining polyurethane foam can generate fine dust particles that may pose health risks if inhaled. It is recommended to use dust collection systems or work in well-ventilated areas to minimize exposure to airborne particles during machining operations.
Surface Finish
To achieve a smooth surface finish on machined polyurethane foam parts, consider using finishing techniques such as sanding, buffing, or coating. These methods can enhance the aesthetics and functionality of the final product.
Safety Precautions
Ensure that proper safety precautions are followed when machining polyurethane foam, including wearing personal protective equipment such as goggles, gloves, and respiratory masks. Additionally, adhere to machine-specific safety guidelines to prevent accidents or injuries.
By employing suitable cutting tools, adjusting speed and feed rates appropriately, controlling dust exposure, focusing on surface finish quality, and prioritizing safety measures, manufacturers can effectively machine polyurethane foam to meet their specific requirements.
8 Essential Tips for Machining Polyurethane Foam with Precision and Safety
- Use sharp cutting tools to achieve clean cuts.
- Maintain proper cutting speeds to prevent melting of the foam.
- Secure the workpiece firmly to avoid vibrations during machining.
- Consider using CNC machines for precision and efficiency.
- Wear appropriate personal protective equipment, such as goggles and gloves.
- Regularly inspect and replace cutting tools to ensure quality cuts.
- Implement dust collection systems to manage foam particles created during machining.
- Experiment with different cutting depths and speeds to find the optimal settings for your specific foam material.
Use sharp cutting tools to achieve clean cuts.
Using sharp cutting tools is essential when machining polyurethane foam to ensure clean and precise cuts. Dull tools can cause tearing, rough edges, and uneven surfaces, leading to a decrease in the quality of the machined parts. By utilizing sharp cutting tools, manufacturers can achieve smooth finishes, accurate dimensions, and improved overall product quality. Additionally, sharp tools reduce the risk of material deformation and help optimize the machining process for greater efficiency and consistency.
Maintain proper cutting speeds to prevent melting of the foam.
Maintaining proper cutting speeds is crucial when machining polyurethane foam to prevent the material from melting. Polyurethane foam is sensitive to heat, and excessive cutting speeds can generate friction that leads to the melting of the foam instead of producing clean cuts. By controlling the cutting speed within the recommended range, manufacturers can ensure precise machining results without compromising the integrity of the foam material. This tip helps in achieving high-quality machined parts while avoiding potential issues such as deformation or surface imperfections caused by overheating.
Secure the workpiece firmly to avoid vibrations during machining.
It is crucial to securely fasten the workpiece during the machining of polyurethane foam to prevent vibrations that can compromise the accuracy and quality of the cuts. By ensuring a stable and firm hold on the workpiece, manufacturers can maintain precision in machining operations, reduce material wastage, and enhance overall productivity. Securely clamping or fixing the workpiece also promotes operator safety by minimizing the risk of unexpected movements or displacements during the machining process.
Consider using CNC machines for precision and efficiency.
When machining polyurethane foam, a valuable tip to enhance precision and efficiency is to consider using CNC machines. CNC (Computer Numerical Control) machines offer unmatched accuracy and repeatability in cutting operations, ensuring consistent results across multiple workpieces. By programming the CNC machine with the desired cutting parameters, intricate shapes and contours can be achieved with ease. This technology not only streamlines the machining process but also minimizes material waste, making it an ideal choice for industries seeking high-quality production of polyurethane foam components.
Wear appropriate personal protective equipment, such as goggles and gloves.
It is crucial to prioritize safety when machining polyurethane foam by wearing appropriate personal protective equipment, such as goggles and gloves. Goggles protect the eyes from potential debris or particles that may be generated during the machining process, while gloves provide a barrier against direct contact with sharp tools or hot surfaces. By ensuring that proper protective gear is worn, operators can safeguard themselves from potential hazards and minimize the risk of injuries while working with polyurethane foam.
Regularly inspect and replace cutting tools to ensure quality cuts.
Regularly inspecting and replacing cutting tools is a crucial tip to ensure quality cuts when machining polyurethane foam. Over time, cutting tools can wear out or become dull, leading to imprecise cuts, rough edges, and increased friction during machining operations. By maintaining sharp and well-maintained cutting tools, manufacturers can achieve consistent and precise results while minimizing the risk of damaging the polyurethane foam material. It is essential to prioritize tool maintenance as part of the machining process to uphold product quality and efficiency in foam fabrication.
Implement dust collection systems to manage foam particles created during machining.
Implementing dust collection systems is a crucial tip to manage foam particles created during machining polyurethane foam. These systems help in capturing and containing the fine dust particles generated during the machining process, reducing the risk of airborne particle exposure. By effectively managing foam particles through dust collection systems, manufacturers can create a safer and healthier working environment while also maintaining the cleanliness of their machining area.
Experiment with different cutting depths and speeds to find the optimal settings for your specific foam material.
When machining polyurethane foam, it is advisable to experiment with various cutting depths and speeds to determine the optimal settings for your particular foam material. By adjusting the cutting depth and speed, you can achieve precise cuts and minimize any potential issues such as tearing or overheating during the machining process. This trial-and-error approach allows you to fine-tune the settings to match the characteristics of your specific foam material, ensuring efficient and accurate machining results.
Hi there! This iss my first comment here sso I just
wanted tto gve a quiick shoujt ouut and say I genuinely enmjoy reading through your posts.
Caan you suggest anny other blogs/websites/forums that covedr the samne
topics? Thanks a ton!
Thank you for your comment! We’re glad to hear that you enjoy reading our posts about machining polyurethane foam. If you’re looking for more resources on similar topics, we recommend checking out industry-specific forums, material processing websites, or technical blogs that focus on manufacturing and fabrication techniques. Feel free to explore these platforms to expand your knowledge and discover additional insights related to machining polyurethane foam. Thank you for being a part of our community!