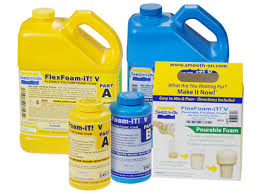
The Versatility of Flex Foam IT III Flexible Polyurethane Foam
Flex Foam IT III flexible polyurethane foam is a versatile material that finds applications in various industries due to its exceptional properties and flexibility. Whether you are in the automotive, furniture, bedding, or packaging industry, Flex Foam IT III offers a wide range of benefits that make it a preferred choice for many manufacturers.
Comfort and Durability
One of the key advantages of Flex Foam IT III is its ability to provide both comfort and durability. In the furniture and bedding industry, this foam is used to create soft yet supportive cushions and mattresses that offer long-lasting comfort to users.
Customizable Solutions
Flex Foam IT III can be easily customized to meet specific requirements. Manufacturers can adjust the density, firmness, and thickness of the foam to suit different applications. This flexibility makes it ideal for creating tailored solutions for diverse products.
Impact Resistance
In the automotive industry, Flex Foam IT III is valued for its excellent impact resistance properties. It helps enhance the safety features of vehicles by providing cushioning in critical areas such as seat padding and headrests.
Insulation and Protection
Flex Foam IT III also serves as an effective insulating material, making it suitable for use in packaging applications. It provides protection against impact during shipping while maintaining product integrity by preventing damage from external factors.
Sustainability
As sustainability becomes increasingly important in manufacturing processes, Flex Foam IT III stands out for its eco-friendly characteristics. It can be recycled and reused, reducing waste and promoting a more sustainable approach to production.
In conclusion, Flex Foam IT III flexible polyurethane foam offers a winning combination of comfort, durability, customization options, impact resistance, insulation capabilities, and sustainability. Its versatility makes it a valuable asset across multiple industries where high-quality flexible foam solutions are required.
Essential Tips for Crafting with Flex Foam IT III: Mastering Flexible Polyurethane Foam
- Flex Foam IT III is a flexible polyurethane foam that can be used for various crafting projects.
- Before using Flex Foam IT III, make sure to read and follow the manufacturer’s instructions carefully.
- To achieve desired flexibility and density, experiment with different mixing ratios of Part A and Part B of Flex Foam IT III.
- Use a digital scale for accurate measurements when mixing Flex Foam IT III components.
- Allow Flex Foam IT III to cure completely according to the recommended time before demolding or further handling your project.
- Ensure proper ventilation when working with Flex Foam IT III as it may release fumes during mixing and curing.
- Store unused portions of Flex Foam IT III in a cool, dry place away from direct sunlight and moisture.
- Clean up any spills or uncured foam promptly using acetone or mineral spirits.
Flex Foam IT III is a flexible polyurethane foam that can be used for various crafting projects.
Flex Foam IT III is a versatile flexible polyurethane foam that lends itself well to a wide range of crafting projects. Whether you are creating intricate sculptures, comfortable cushions, or unique props, this foam offers the flexibility and durability needed to bring your creative ideas to life. Its ease of manipulation and ability to hold shape make it an excellent choice for crafters looking to add dimension and depth to their projects with a material that is both reliable and easy to work with.
Before using Flex Foam IT III, make sure to read and follow the manufacturer’s instructions carefully.
It is essential to prioritize safety and efficiency when working with Flex Foam IT III flexible polyurethane foam. Before using this versatile material, it is crucial to carefully read and adhere to the manufacturer’s instructions. Following the guidelines provided ensures that you achieve the best results and maintain the quality and performance of the foam. By following the recommended instructions, you can optimize your use of Flex Foam IT III and ensure that your projects are successful.
To achieve desired flexibility and density, experiment with different mixing ratios of Part A and Part B of Flex Foam IT III.
To attain the desired flexibility and density in Flex Foam IT III flexible polyurethane foam, it is recommended to experiment with various mixing ratios of Part A and Part B components. By adjusting the proportions of these two parts during the mixing process, manufacturers can fine-tune the characteristics of the foam to meet specific requirements for different applications. This flexibility allows for customization and optimization of the foam’s properties, ensuring that it performs effectively in various settings across industries.
Use a digital scale for accurate measurements when mixing Flex Foam IT III components.
For precise and consistent results when working with Flex Foam IT III flexible polyurethane foam, it is essential to use a digital scale for accurate measurements while mixing its components. By carefully weighing the components according to the recommended ratios, you can ensure that the foam cures properly and achieves the desired properties. Using a digital scale eliminates guesswork and helps maintain quality control throughout the mixing process, leading to reliable and high-performance foam applications.
Allow Flex Foam IT III to cure completely according to the recommended time before demolding or further handling your project.
It is crucial to allow Flex Foam IT III flexible polyurethane foam to cure completely within the recommended time frame before demolding or proceeding with any further handling of your project. By following this tip, you ensure that the foam reaches its optimal strength and performance characteristics, leading to a successful end result. Rushing the curing process may compromise the integrity of the foam and impact its overall quality and durability. Patience in allowing the foam to cure fully will ultimately contribute to the longevity and effectiveness of your project.
Ensure proper ventilation when working with Flex Foam IT III as it may release fumes during mixing and curing.
It is crucial to ensure proper ventilation when working with Flex Foam IT III flexible polyurethane foam as it may release fumes during the mixing and curing process. Adequate ventilation helps to dissipate any potentially harmful fumes, ensuring a safe working environment for individuals handling the foam. By following this precautionary measure, you can minimize exposure to fumes and maintain a healthy workspace while utilizing the benefits of Flex Foam IT III for your projects.
Store unused portions of Flex Foam IT III in a cool, dry place away from direct sunlight and moisture.
For optimal storage of unused portions of Flex Foam IT III flexible polyurethane foam, it is recommended to keep them in a cool, dry place away from direct sunlight and moisture. Storing the foam in these conditions helps maintain its quality and extend its shelf life. Exposure to sunlight and moisture can affect the properties of the foam, leading to potential changes in performance and durability. By following this simple tip, you can ensure that your Flex Foam IT III remains in top condition for future use.
Clean up any spills or uncured foam promptly using acetone or mineral spirits.
It is essential to clean up any spills or uncured Flex Foam IT III flexible polyurethane foam promptly using acetone or mineral spirits. These solvents are effective in removing the foam before it cures and hardens, making cleanup easier and preventing any unwanted adhesion to surfaces. By following this tip, you can maintain a clean work environment and ensure proper application of the foam for optimal results.