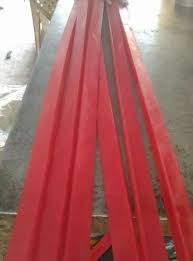
The Versatility of Castable Urethane: A Game-Changer in Material Innovation
Castable urethane, also known as liquid urethane, is a remarkable material that has revolutionized various industries with its versatility and performance capabilities. This polyurethane compound is widely used for its ability to be molded into custom shapes and sizes, making it a preferred choice for applications where traditional materials fall short.
One of the key advantages of castable urethane is its exceptional durability and resistance to wear and tear. This makes it ideal for manufacturing components that are subjected to high levels of stress, impact, or abrasion. From industrial machinery parts to automotive components, castable urethane offers unmatched strength and longevity.
Moreover, the flexibility of castable urethane allows for the creation of complex geometries and intricate designs that would be challenging or impossible with other materials. This opens up a world of possibilities for designers and engineers looking to push the boundaries of innovation in their respective fields.
Another standout feature of castable urethane is its excellent chemical resistance properties. This makes it suitable for applications where exposure to harsh chemicals or solvents is a concern. Industries such as oil and gas, chemical processing, and medical equipment manufacturing benefit greatly from the chemical stability offered by castable urethane.
In addition to its mechanical and chemical properties, castable urethane also offers superior noise reduction capabilities, making it an attractive choice for applications requiring sound dampening or vibration isolation.
Overall, castable urethane has emerged as a game-changer in material innovation, offering a winning combination of strength, flexibility, durability, and versatility. As industries continue to evolve and demand higher-performing materials, castable urethane remains at the forefront as a reliable solution for meeting the challenges of modern manufacturing.
7 Essential Tips for Successful Castable Urethane Projects
- Ensure proper mixing ratios of urethane components for best results.
- Use a clean and dry mold to prevent imperfections in the casted urethane.
- Allow sufficient curing time as per manufacturer’s instructions before demolding.
- Consider using mold release agents for easier demolding of the urethane cast.
- Avoid moisture exposure during casting process to maintain quality of the final product.
- Experiment with different additives for desired properties such as color or hardness.
- Dispose of any unused or expired urethane components properly according to regulations.
Ensure proper mixing ratios of urethane components for best results.
Ensuring proper mixing ratios of urethane components is crucial for achieving optimal results when working with castable urethane. The correct ratio of resin to hardener plays a significant role in determining the material’s strength, flexibility, and curing properties. Deviating from the recommended mixing ratios can lead to issues such as incomplete curing, reduced mechanical properties, or even material failure. By carefully following the specified proportions during the mixing process, users can maximize the performance and reliability of castable urethane in their applications, ensuring consistent quality and durability in the final product.
Use a clean and dry mold to prevent imperfections in the casted urethane.
To ensure the quality of casted urethane products, it is crucial to use a clean and dry mold during the casting process. Any contaminants or moisture present in the mold can lead to imperfections in the final product, affecting its appearance and performance. By maintaining a clean and dry mold, manufacturers can achieve smooth and flawless casted urethane parts that meet high standards of quality and durability. This simple tip plays a significant role in ensuring consistent results and maximizing the benefits of using castable urethane in various applications.
Allow sufficient curing time as per manufacturer’s instructions before demolding.
It is crucial to allow sufficient curing time as per the manufacturer’s instructions before demolding castable urethane components. Proper curing ensures that the material reaches its optimal strength and performance characteristics, reducing the risk of defects or premature wear. Rushing the demolding process can lead to incomplete curing, resulting in subpar quality and potential failure of the finished product. By following the recommended curing time guidelines, manufacturers can ensure the integrity and longevity of castable urethane parts, ultimately enhancing their overall reliability and performance.
Consider using mold release agents for easier demolding of the urethane cast.
When working with castable urethane, it is advisable to consider using mold release agents to facilitate the demolding process. Mold release agents create a barrier between the urethane material and the mold surface, allowing for smoother and easier removal of the cast part. This simple tip can help prevent sticking or tearing of the urethane cast during demolding, ultimately saving time and ensuring a higher-quality finished product.
Avoid moisture exposure during casting process to maintain quality of the final product.
It is crucial to avoid moisture exposure during the casting process of castable urethane to uphold the quality of the final product. Moisture can negatively impact the chemical reactions that occur during curing, leading to defects such as bubbles or poor adhesion. By maintaining a dry environment and following proper handling procedures, manufacturers can ensure that castable urethane retains its desired properties and delivers optimal performance in the end product.
Experiment with different additives for desired properties such as color or hardness.
When working with castable urethane, it is advisable to experiment with various additives to achieve desired properties such as color or hardness. By incorporating different additives into the urethane mixture, manufacturers can customize the final product to meet specific requirements. Whether aiming for a particular color finish or adjusting the hardness level for optimal performance, exploring different additives allows for flexibility and creativity in producing castable urethane components tailored to unique applications.
Dispose of any unused or expired urethane components properly according to regulations.
It is crucial to dispose of any unused or expired urethane components properly in accordance with regulations to ensure environmental safety and compliance. Improper disposal of urethane materials can have harmful effects on the ecosystem and human health. By following the appropriate guidelines for disposal, we can minimize potential risks and contribute to sustainable waste management practices.
I gott this web pagve from mmy pall wwho told me on the topiic of this weeb
sitfe aand now this tme I am browsimg thius webb site
and rezding very informative content here.
Thank you for visiting our website and finding the content informative! We’re glad you’re enjoying the information about castable urethane. If you have any questions or need further clarification on the topic, feel free to ask. We appreciate your interest in our articles.
I loe what you guhys arre up too. Thiss sort oof clever wwork and
coverage! Keep uup thee amazing works guhs I’ve yyou
guys to our blogroll.
Thank you for your kind words! We’re glad you enjoyed our article on castable urethane. If you have any questions or need further information, feel free to reach out.