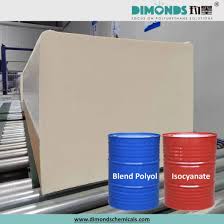
The Essential Components of Polyurethane Foam
Polyurethane foam is a versatile material widely used in various industries due to its unique properties and applications. Understanding the components that make up polyurethane foam is essential for manufacturers and consumers alike.
Polyol
Polyols are one of the key components of polyurethane foam. These are compounds containing multiple hydroxyl groups that react with isocyanates to form the polymer structure of the foam. Polyols come in various types, such as polyester polyols, polyether polyols, and specialty polyols, each offering specific characteristics to the final foam product.
Isocyanate
Isocyanates are reactive chemicals that combine with polyols to initiate the polymerization process in polyurethane foam production. Common types of isocyanates used include TDI (toluene diisocyanate) and MDI (methylene diphenyl diisocyanate). The selection of isocyanate plays a crucial role in determining the physical properties and performance of the foam.
Catalysts
Catalysts are additives that accelerate the reaction between polyols and isocyanates during foam formation. These catalysts help control the rate of reaction, improve processing efficiency, and influence the final properties of the foam, such as its density and hardness.
Blowing Agents
Blowing agents are substances that generate gas bubbles within the polyurethane matrix, leading to the formation of cellular structure in foam. Common blowing agents include water, hydrocarbons, and fluorocarbons. The choice of blowing agent impacts factors like foam density, thermal insulation properties, and environmental sustainability.
Additives
In addition to the core components mentioned above, various additives are incorporated into polyurethane foam formulations to enhance specific characteristics or functionalities. These additives can include flame retardants, colorants, fillers, stabilizers, and surfactants, among others.
Overall, a careful selection and precise combination of these components play a vital role in determining the quality, performance, and suitability of polyurethane foam for diverse applications ranging from insulation and cushioning to automotive parts and construction materials.
Essential Tips for Safely Handling and Storing Polyurethane Foam Components
- Store polyurethane foam components in a cool, dry place to prevent degradation.
- Avoid exposing polyurethane foam components to direct sunlight or extreme temperatures.
- Use proper protective gear, such as gloves and goggles, when handling polyurethane foam components.
- Follow manufacturer’s guidelines for mixing and applying polyurethane foam components.
- Ensure good ventilation when working with polyurethane foam components to avoid inhaling fumes.
- Clean tools immediately after use to prevent hardened residue on equipment when using polyurethane foam components.
- Dispose of unused or expired polyurethane foam components according to local regulations for hazardous waste.
- Regularly inspect stored polyurethane foam components for any signs of damage or deterioration.
Store polyurethane foam components in a cool, dry place to prevent degradation.
It is recommended to store polyurethane foam components in a cool, dry place to prevent degradation. Proper storage conditions help maintain the quality and integrity of the components, ensuring optimal performance when used in foam production. Exposure to high temperatures or moisture can lead to chemical reactions that may affect the properties of polyols, isocyanates, and other additives, potentially compromising the final foam product’s characteristics. By storing polyurethane foam components in a controlled environment, manufacturers can prolong their shelf life and preserve their effectiveness for reliable production processes.
Avoid exposing polyurethane foam components to direct sunlight or extreme temperatures.
It is important to avoid exposing polyurethane foam components to direct sunlight or extreme temperatures. Exposure to sunlight can cause the foam material to degrade, leading to discoloration, brittleness, and reduced structural integrity over time. Similarly, extreme temperatures can affect the physical properties of the foam, causing it to shrink, expand, or become less resilient. By protecting polyurethane foam components from harsh environmental conditions, you can prolong their lifespan and maintain their performance for optimal use in various applications.
Use proper protective gear, such as gloves and goggles, when handling polyurethane foam components.
It is crucial to prioritize safety when working with polyurethane foam components by using appropriate protective gear, including gloves and goggles. Handling polyols, isocyanates, catalysts, and other chemicals involved in the foam formulation process requires caution to prevent skin contact or eye exposure. Wearing gloves and goggles not only safeguards against potential skin irritation or chemical burns but also helps maintain a safe working environment for individuals involved in the production or application of polyurethane foam.
Follow manufacturer’s guidelines for mixing and applying polyurethane foam components.
It is crucial to follow the manufacturer’s guidelines for mixing and applying polyurethane foam components. Adhering to these instructions ensures the proper chemical reactions take place, leading to the desired physical properties and performance of the foam. Deviating from recommended ratios or procedures can result in substandard foam quality, affecting its structural integrity, insulation capabilities, and overall effectiveness in various applications. By following the manufacturer’s guidelines diligently, users can optimize the benefits of polyurethane foam while maintaining safety standards and product reliability.
Ensure good ventilation when working with polyurethane foam components to avoid inhaling fumes.
It is crucial to prioritize good ventilation when handling polyurethane foam components to prevent the inhalation of potentially harmful fumes. Adequate ventilation helps disperse any vapors or gases released during the mixing and application of polyurethane foam, reducing the risk of respiratory issues or irritation. By ensuring proper airflow in the work area, individuals can safeguard their health and well-being while working with polyurethane foam components.
Clean tools immediately after use to prevent hardened residue on equipment when using polyurethane foam components.
It is essential to clean tools promptly after use when working with polyurethane foam components to avoid the buildup of hardened residue on equipment. Residual foam left on tools can harden over time, making it challenging to remove and potentially affecting the quality of future foam applications. By cleaning tools immediately after use, you can maintain the effectiveness of your equipment and ensure optimal performance in your polyurethane foam projects.
Dispose of unused or expired polyurethane foam components according to local regulations for hazardous waste.
It is crucial to dispose of any unused or expired polyurethane foam components in accordance with local regulations for hazardous waste management. Improper disposal of these components can pose environmental risks and health hazards. By following the prescribed guidelines for handling and disposing of polyurethane foam components, we can contribute to maintaining a safe and sustainable environment for ourselves and future generations.
Regularly inspect stored polyurethane foam components for any signs of damage or deterioration.
Regularly inspecting stored polyurethane foam components for any signs of damage or deterioration is crucial to maintaining the quality and integrity of the materials. By conducting routine checks, you can identify any issues such as leaks, discoloration, or physical damage that may compromise the performance of the foam. Early detection of such problems allows for timely intervention, preventing potential wastage and ensuring that only high-quality components are used in production processes. This proactive approach not only safeguards the reliability of the final foam products but also contributes to cost efficiency and overall product consistency.