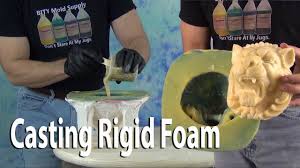
The Advantages of Rigid Foam Casting in Industrial Applications
Rigid foam casting is a versatile and cost-effective process that plays a crucial role in various industrial applications. This method involves pouring a liquid mixture of resin and hardener into a mold, where it expands and solidifies to form a rigid foam structure. Here are some key advantages of using rigid foam casting:
Lightweight yet Durable
Rigid foam castings are known for their lightweight properties, making them ideal for applications where weight reduction is essential. Despite being lightweight, these castings offer excellent durability and structural integrity, making them suitable for demanding industrial environments.
Precision and Consistency
One of the main benefits of rigid foam casting is its ability to produce parts with intricate details and precise dimensions. The molding process allows for consistent replication of complex shapes, ensuring uniformity across multiple parts.
Thermal Insulation
Rigid foam castings exhibit excellent thermal insulation properties, making them valuable in applications where temperature control is critical. These castings can help maintain stable operating temperatures and protect sensitive components from heat or cold exposure.
Chemical Resistance
Many rigid foam materials used in casting processes offer high chemical resistance, making them suitable for applications where exposure to corrosive substances is common. This resistance ensures the longevity and reliability of components even in harsh chemical environments.
Cost-Effective Production
Rigid foam casting is a cost-effective manufacturing process compared to traditional methods such as machining or injection molding. The ability to produce complex shapes with minimal material waste makes this process efficient for both small-scale production runs and large-volume manufacturing.
In conclusion, rigid foam casting offers a wide range of advantages that make it an attractive choice for various industrial applications. From lightweight design to precision molding capabilities, this method provides manufacturers with a versatile solution for producing high-quality components efficiently and cost-effectively.
5 Essential Tips for Safe and Effective Rigid Foam Casting
- Ensure proper ventilation when working with rigid foam casting materials.
- Follow manufacturer’s instructions for mixing and pouring the foam resin accurately.
- Use appropriate safety gear such as gloves, goggles, and a mask to protect yourself from fumes and chemicals.
- Allow sufficient curing time for the foam to set and harden before removing it from the mold.
- Consider using release agents on the mold to prevent the foam from sticking and facilitate easy removal.
Ensure proper ventilation when working with rigid foam casting materials.
Proper ventilation is crucial when working with rigid foam casting materials to ensure a safe and healthy working environment. These materials can release fumes or vapors during the casting process, which may pose health risks if inhaled in high concentrations. Adequate ventilation helps to dissipate these potentially harmful substances, reducing the risk of respiratory issues or other health concerns for workers. By prioritizing proper ventilation in the workspace, individuals can safeguard their well-being while engaging in rigid foam casting activities.
Follow manufacturer’s instructions for mixing and pouring the foam resin accurately.
It is crucial to follow the manufacturer’s instructions meticulously when mixing and pouring the foam resin in rigid foam casting. Accurate measurement and proper mixing ratios are essential to ensure the desired chemical reaction takes place, leading to the formation of a strong and stable foam structure. Deviating from the recommended guidelines can result in issues such as incomplete curing, poor structural integrity, or uneven expansion, compromising the quality of the final product. Adhering to the manufacturer’s instructions guarantees optimal performance and consistency in rigid foam casting processes.
Use appropriate safety gear such as gloves, goggles, and a mask to protect yourself from fumes and chemicals.
It is crucial to prioritize safety when engaging in rigid foam casting processes. To ensure personal protection, it is recommended to use appropriate safety gear such as gloves, goggles, and a mask. These safety measures help safeguard against potential hazards posed by fumes and chemicals involved in the casting process. Wearing the right protective equipment not only promotes a safe working environment but also minimizes the risk of exposure to harmful substances, ensuring the well-being of individuals involved in the casting operation.
Allow sufficient curing time for the foam to set and harden before removing it from the mold.
When engaging in rigid foam casting, it is crucial to allow sufficient curing time for the foam to set and harden inside the mold before attempting to remove it. Rushing this process can lead to incomplete curing, resulting in structural weaknesses or deformities in the final product. By exercising patience and ensuring that the foam has fully hardened, you can achieve optimal results with strong and durable castings that meet your quality standards.
Consider using release agents on the mold to prevent the foam from sticking and facilitate easy removal.
When engaging in rigid foam casting, it is advisable to apply release agents on the mold surface before pouring the foam mixture. These release agents serve as a protective barrier that prevents the foam from adhering to the mold, making it easier to remove the finished casting once it has solidified. By using release agents effectively, manufacturers can ensure smooth demolding processes, reduce the risk of damage to the castings, and maintain the integrity of both the molds and the final products.