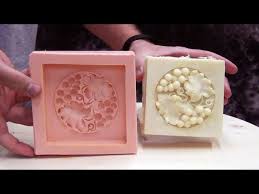
The Versatility of Flexible Casting Foam in Various Industries
Flexible casting foam is a versatile material that finds applications across a wide range of industries due to its unique properties and characteristics. This type of foam is known for its flexibility, durability, and ability to conform to different shapes, making it ideal for various casting and molding processes.
Automotive Industry
In the automotive industry, flexible casting foam is commonly used for creating seat cushions, armrests, headrests, and other interior components. Its ability to provide comfort, support, and impact resistance makes it a preferred choice for enhancing the overall driving experience.
Furniture Manufacturing
Manufacturers in the furniture industry utilize flexible casting foam to create cushioning materials for sofas, chairs, mattresses, and other upholstered furniture pieces. The foam’s resilience and softness contribute to the comfort and longevity of these products.
Arts and Crafts
Artists and craftsmen often use flexible casting foam in their projects to create intricate designs and sculptures. The foam’s moldability allows for detailed replication of shapes and textures, making it a popular choice for art installations and decorative pieces.
Medical Equipment
In the healthcare sector, flexible casting foam plays a crucial role in the manufacturing of medical equipment such as prosthetics, orthopedic supports, padding materials, and custom-fitted devices. Its hypoallergenic properties and customizable nature make it suitable for sensitive applications.
Sports Equipment
Sports equipment manufacturers rely on flexible casting foam to produce protective gear like helmets, padding inserts, shin guards, and ergonomic grips. The foam’s shock-absorbing capabilities help reduce impact-related injuries during athletic activities.
Overall, flexible casting foam continues to be an indispensable material across multiple industries due to its versatility, reliability, and adaptability to diverse manufacturing requirements. Its ability to enhance product performance while ensuring user comfort makes it a preferred choice for many applications.
9 Essential Tips for Successful Flexible Casting Foam Projects
- Ensure proper ventilation when working with flexible casting foam.
- Follow the manufacturer’s instructions for mixing the foam components accurately.
- Use a mold release agent to prevent the foam from sticking to the mold.
- Allow sufficient curing time as per the product specifications before demolding.
- Avoid overfilling the mold to prevent excess foam spillage.
- Wear appropriate protective gear, such as gloves and goggles, when handling the foam.
- Store the foam components in a cool, dry place away from direct sunlight.
- Test a small batch of foam first to understand its expansion properties before large-scale use.
- Clean up spills or uncured foam immediately using recommended solvents.
Ensure proper ventilation when working with flexible casting foam.
It is crucial to ensure proper ventilation when working with flexible casting foam. Adequate ventilation helps to minimize exposure to potentially harmful fumes that may be released during the casting process. By working in a well-ventilated area, you can protect yourself from inhaling any airborne particles and maintain a safe and healthy work environment. Proper ventilation not only promotes personal safety but also ensures the quality of the casting foam products being produced.
Follow the manufacturer’s instructions for mixing the foam components accurately.
It is crucial to adhere to the manufacturer’s instructions when mixing the components of flexible casting foam accurately. Following the prescribed guidelines ensures the proper chemical reaction and consistency of the foam, leading to optimal performance and desired physical properties in the final product. By carefully measuring and blending the foam components as directed, users can achieve reliable results, consistent quality, and avoid potential issues such as uneven expansion or inadequate curing.
Use a mold release agent to prevent the foam from sticking to the mold.
Using a mold release agent is a crucial tip when working with flexible casting foam to prevent it from sticking to the mold. By applying a proper mold release agent before pouring the foam into the mold, you ensure easy removal of the cured foam without damaging the mold or the final product. This simple yet effective step not only saves time and effort but also helps maintain the quality and integrity of your casted items, ensuring smooth and seamless production processes.
Allow sufficient curing time as per the product specifications before demolding.
It is essential to adhere to the recommended curing time specified for flexible casting foam before demolding the final product. Allowing sufficient curing time ensures that the foam sets and cures properly, leading to improved structural integrity and dimensional stability. Rushing the demolding process before the foam has fully cured can result in deformities, surface imperfections, or reduced strength of the finished product. By following the product specifications for curing time, you can achieve optimal results and ensure that the flexible casting foam performs effectively in its intended application.
Avoid overfilling the mold to prevent excess foam spillage.
When working with flexible casting foam, it is important to avoid overfilling the mold to prevent excess foam spillage. Overfilling can lead to wastage of material, messy cleanup, and potential quality issues in the final product. By carefully measuring and pouring the appropriate amount of foam into the mold, you can ensure a clean and efficient casting process while achieving optimal results. Properly managing the filling level helps maintain control over the expansion of the foam and promotes a smooth finish without any unnecessary overflow.
Wear appropriate protective gear, such as gloves and goggles, when handling the foam.
It is essential to prioritize safety when working with flexible casting foam. Always remember to wear appropriate protective gear, such as gloves and goggles, when handling the foam. This precaution helps protect your skin and eyes from potential irritation or harmful chemicals present in the foam. By following this simple tip, you can ensure a safe and secure working environment while effectively utilizing flexible casting foam for your projects.
Store the foam components in a cool, dry place away from direct sunlight.
For optimal performance and longevity of flexible casting foam components, it is recommended to store them in a cool, dry place away from direct sunlight. Exposure to high temperatures or moisture can affect the quality and properties of the foam, leading to potential degradation or deformation. By storing the foam components in a controlled environment, you can ensure that they retain their flexibility, resilience, and overall integrity for use in various applications.
Test a small batch of foam first to understand its expansion properties before large-scale use.
Testing a small batch of flexible casting foam before large-scale use is a crucial tip to ensure successful outcomes in manufacturing processes. By conducting a trial run, manufacturers can gain valuable insights into the foam’s expansion properties, including its rate of expansion and final density. This preliminary testing allows for adjustments to be made to the mixing ratio, curing time, or mold preparation, resulting in more precise and consistent results when scaling up production. Ultimately, this proactive approach helps minimize potential wastage of materials and resources while optimizing the quality of the final products.
Clean up spills or uncured foam immediately using recommended solvents.
To maintain the quality and effectiveness of flexible casting foam, it is essential to clean up spills or uncured foam promptly using the solvents recommended for this purpose. Immediate action helps prevent the foam from hardening and adhering to surfaces, making cleanup more challenging. By following the manufacturer’s guidelines and using appropriate solvents, users can ensure efficient removal of spills or uncured foam, preserving the integrity of their projects and equipment.